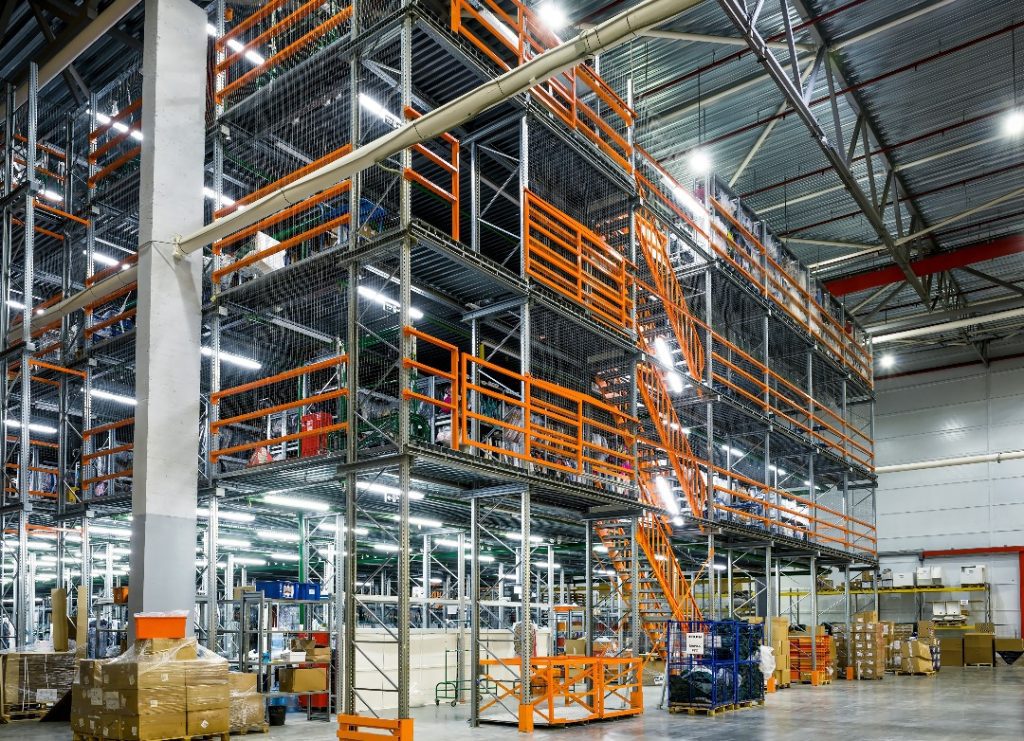
Custom Racking in Malaysia: You Need It?
Why Custom Racking is the Key to Modern Warehouse Efficiency
Custom Racking is essential for transforming warehouse operations. In today’s fast-paced business environment, using one-size-fits-all storage solutions can lead to wasted space and increased costs. Instead, Custom Racking – or tailored storage systems – is designed to meet your specific needs, ensuring that every square inch of your facility works for you.
Comparing Standard vs. Custom Racking Solutions
When choosing between standard and custom storage, it is important to understand the key differences. Custom Racking is engineered to optimize space and improve workflow, whereas standard systems often come with fixed dimensions. Moreover, custom solutions offer:
Factor | Standard Racking | Custom Racking |
---|---|---|
Cost | Lower upfront cost | Higher initial investment; long-term ROI is superior |
Deployment Time | Immediate availability | Longer lead time due to personalized design |
Scalability | Limited adaptability | Modular designs that evolve with your business |
Space Utilization | Fixed dimensions that leave gaps | Maximizes vertical and horizontal space effectively |
Compatibility | Generic for basic needs | Tailored to specific equipment, SKUs, and processes |
Additionally, with Custom Racking, you benefit from a solution that precisely addresses your storage challenges.
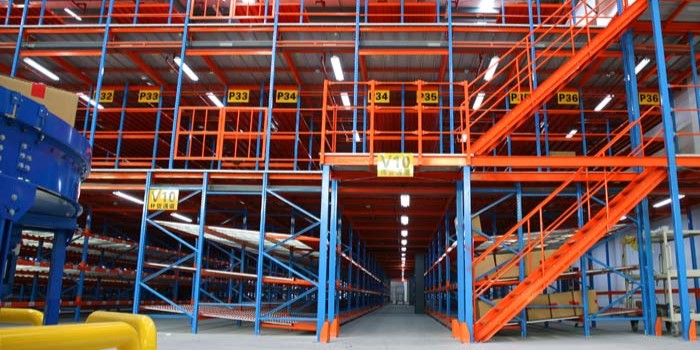
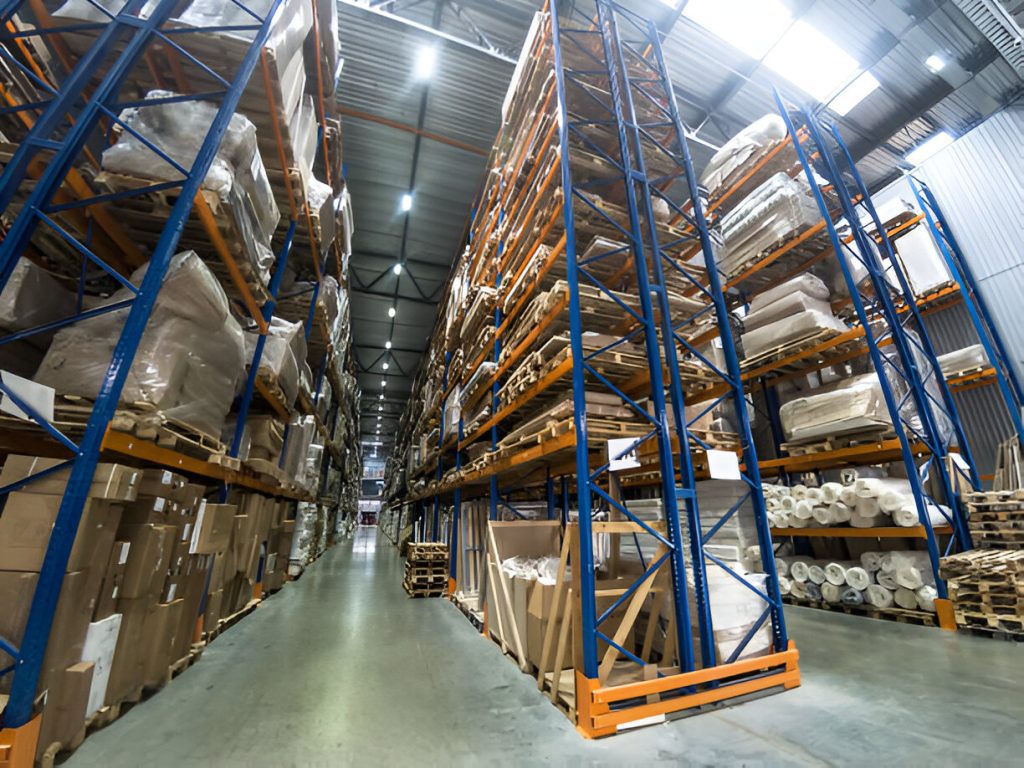
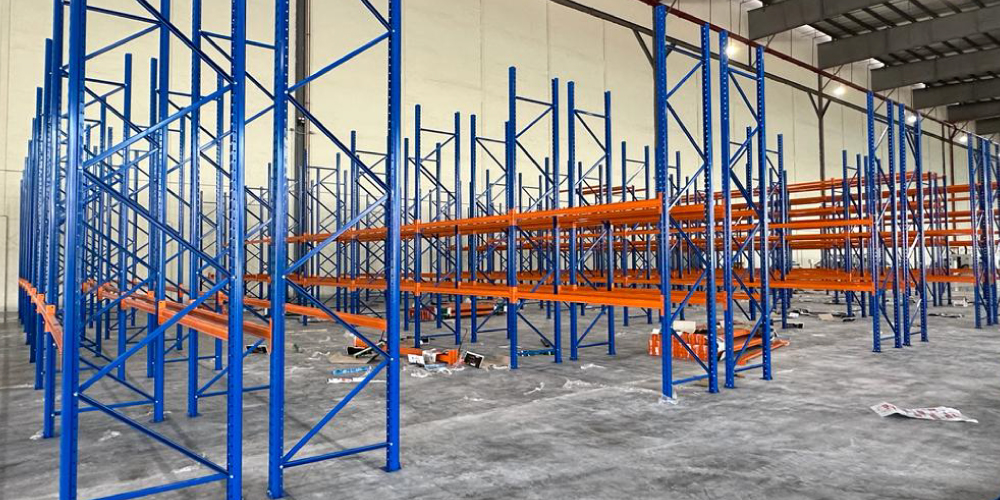
Need a custom racking setup like these? Let’s make it happen.
You’ve seen the mess. You’ve dealt with the frustration. But what if your racking was built EXACTLY for what you need? No compromises. No wasted storage. Just a perfect fit—like these real projects we’ve completed for businesses just like yours.
Industry-Specific Custom Racking Benefits
Food & Beverage: Freshness and Compliance
- Custom FIFO Racking: Ensures that perishables rotate correctly, reducing food waste by up to 20%.
- Special Coatings: Anti-corrosion finishes are essential in cold storage, preventing frost buildup and ensuring hygiene.
- Case in Point: One cold storage facility saw a 15% decrease in spoilage after adopting custom cantilever racking for bulky produce.
Automotive: Heavy-Duty, Precise Storage
- Engineered for Strength: Custom steel pallet racks can support up to 5,000 lbs per shelf.
- Adjustable Shelving: Tailored small-bin solutions organize parts like bolts and fasteners, cutting picking times by 25%.
- In Addition: Custom designs accommodate irregular automotive parts, boosting both safety and efficiency.
Pharmaceuticals: Safety and Compliance
- Temperature Zones: Custom racking integrated with HVAC systems keeps medications at optimal temperatures.
- Secure Systems: Features such as tamper-proof locks ensure compliance with FDA guidelines.
- Moreover: These systems enhance safety by minimizing risks of cross-contamination.
E-Commerce: Speed and Flexibility
- Modular Shelving: Custom, modular designs easily adapt to seasonal fluctuations without downtime.
- Multi-Tier Systems: These systems streamline order fulfillment, reducing picking time by up to 40%.
- Also: Custom Racking allows for quick reconfiguration in response to inventory changes.
Future-Proofing Your Warehouse
Scalability Options
- Vertical Expansion: By adding mezzanine floors, you can double your storage capacity without enlarging your facility.
- Automation Integration: Custom systems can be built to work with automated storage and retrieval systems, enhancing efficiency.
- Quick Reconfiguration: Unlike standard systems, custom designs can be adjusted in days rather than weeks, ensuring minimal disruption.
Data-Driven ROI Analysis
Before making a decision, work with providers who offer robust ROI analysis. By modeling layout changes and analyzing space utilization, you can:
- Identify the most efficient configuration.
- Predict potential savings from reduced labor and better space utilization.
- Ensure long-term benefits justify the initial investment.
Selecting the Right Custom Racking Provider
When evaluating providers, consider these four essential factors:
Material Quality and Safety
- Durability: Look for high-quality, powder-coated steel that lasts over 15 years.
- Safety Compliance: The system must meet OSHA/ANSI standards for load limits and seismic stability.
Comprehensive Support
- Installation and Maintenance: A good provider offers end-to-end support, ensuring smooth installation and ongoing maintenance.
- Customer Service: Prompt communication is vital to resolve issues quickly and minimize downtime.
Industry Expertise
- Specialization: Providers with experience in your industry can offer tailored advice that generic suppliers may miss.
- Proven Success: Request case studies as well as testimonials to verify their track record with similar projects.
Balanced Customization
- Tailored Solutions: Ensure the provider offers designs that are truly customized, rather than simply repackaging standard options.
- Future Growth: The system should be scalable and adaptable to evolving business needs.
Don’t settle for the wrong racking. Get it done right
Not all racking providers are the same. The wrong choice? Wasted space, weak racks, and a whole lot of regret. Here’s how to pick the right one.
Beyond Storage: The Broader Benefits
Improved Workflow and Employee Efficiency
By optimizing layouts with Custom Racking, every aisle and shelf is designed for maximum efficiency. Consequently, employees can pick orders faster, which leads to:
- Faster Order Fulfillment: Reduced travel time increases productivity.
- Ergonomic Design: Custom heights and configurations reduce worker strain.
Enhanced Inventory Management
Custom systems can integrate with Warehouse Management Systems (WMS) and tracking technologies. For example:
- Real-Time Monitoring: Automated systems provide immediate updates on stock levels.
- Reduced Errors: Better organization means fewer misplaced items. Above all, it keeps accurate inventory counts.
Sustainability and Long-Term Savings
Using Custom Racking maximizes space without the need for costly warehouse expansions. Moreover:
- Energy Efficiency: Optimized space reduces the need for additional lighting and cooling.
- Durability: Although the upfront cost is higher, the long-term maintenance and replacement costs are significantly lower.
Integration with Advanced Technologies
Custom Racking systems can be designed to integrate with modern automation and robotics, offering:
- Seamless Automation: Integration with AS/RS systems as a result it will boosts efficiency.
- Smart Analytics: Sensors and IoT devices monitor load capacities and provide predictive maintenance alerts. However, please make sure to make comprehensive preparation.
Conclusion: Invest in Racking with a Future-Proof Warehouse
In summary, standard racking systems may be less expensive initially, but they cannot match the tailored efficiency of Custom Racking. By maximizing space, enhancing safety, and improving workflow, custom storage solutions lead to significant long-term savings and operational improvements.
Moreover, by investing in Custom Racking, you are not only addressing your current storage needs but also future-proofing your warehouse for growth and technological advancements. Therefore, assess your specific requirements and partner with an experienced provider who can deliver a solution that truly fits your business.
Invest in a tailored, data-driven Custom Racking solution today and experience the transformative benefits for your warehouse operations.
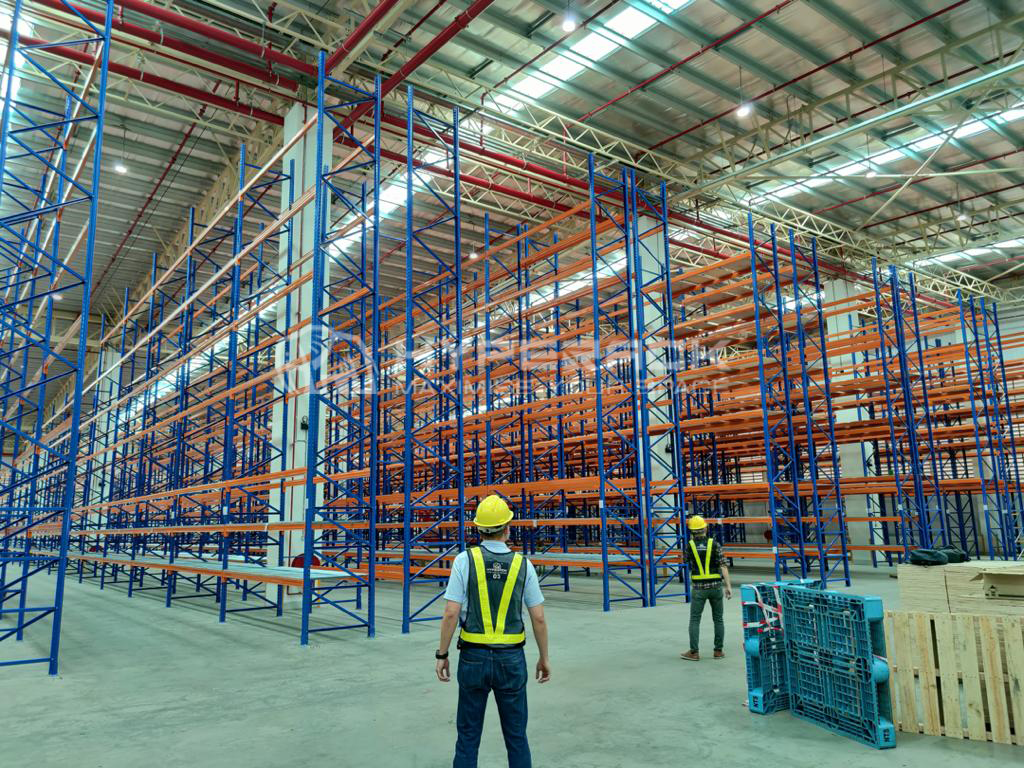
Shelf Racking Supplier: Add-ons / Services You Might Be Missing
What to Ask Your Shelf Racking Supplier
When purchasing a shelf racking system, many businesses tend to focus only on the price, basic specifications and types of racking system. However, overlooking essential add-ons and supplier services—often included or even free—can result in wasted spending. Negotiating with your supplier to include these extras can help avoid costly inefficiencies, safety hazards, and missed opportunities for optimizing your warehouse storage. Obviously, to ensure you get the best value, here’s a guide on what to ask your racking supplier beyond just the racks themselves.
Why You Should Ask for More Than Just the Racks
Investing in a racking system is more than just installing shelves—it’s about maximizing efficiency, safety, and long-term durability. Suppliers often offer valuable additional services and products that improve the usability and lifespan of your storage racking system. By knowing what to request, you can avoid future headaches and optimize your warehouse storage effectively.
Without proper add-ons, your shelf racking system may suffer from:
- Structural weaknesses due to missing protective accessories
- Shorter lifespan due to inadequate coatings or low-quality materials
- Workplace hazards from racks that aren’t properly reinforced
- Difficult upgrades due to a lack of technical drawings or blueprints
- Higher maintenance costs from unanticipated wear and tear
To avoid these pitfalls, consider asking your supplier for these essential products and services.
Essential Shelf Racking Add-ons to Request from Your Supplier
1. Must-Have Racking Safety Accessories
Safety should always be a priority when installing a shelf racking system. Many racking suppliers offer protective accessories that enhance the durability and safety of your storage racks. Be sure to ask for:
- Load Capacity Signs – Clear signage indicating weight limits to prevent overloading.
- Column Protectors – Shields that prevent damage from forklifts or pallet jacks.
- Anti-Collapse Mesh – A barrier placed at the back of racks to prevent items from falling onto workers.
- End-of-Aisle Guards – Additional safety barriers to protect racks from vehicle impact.
- Rack Safety Clips – Ensure beams remain securely locked in place to avoid collapses.
- Rack Netting – Prevents smaller items from falling and causing hazards in high-rack storage.
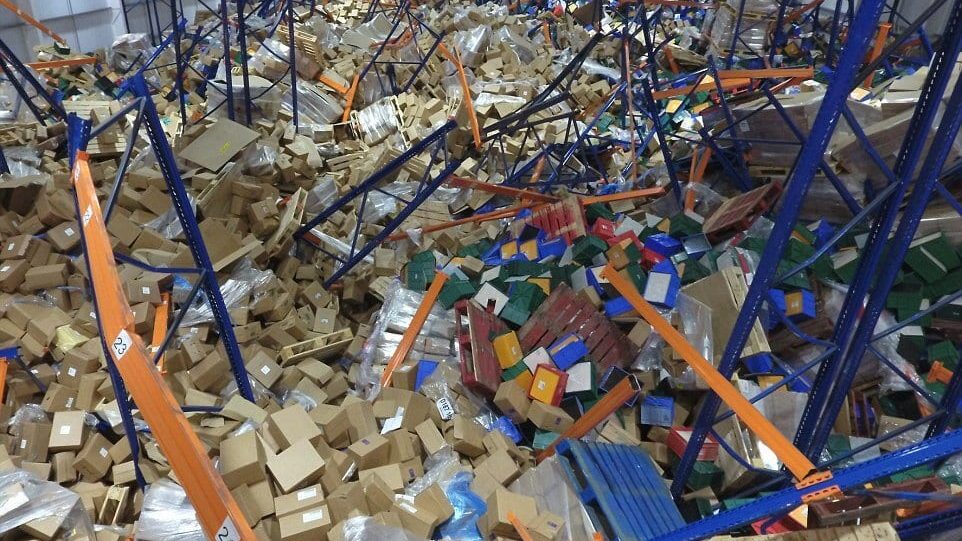
These accessories help minimize damage risks, prevent workplace accidents, as well as extend the lifespan of your shelf racking system.
How Safety Accessories Prevent Costly Accidents;
A case study from a large logistics warehouse revealed that after implementing rack column protectors and anti-collapse mesh, accidents related to falling objects reduced by 40%. Additionally, rack maintenance costs dropped significantly, as minor damages were prevented before they turned into costly repairs.
2. Custom Coating or Material Options for Shelf Racks
Depending on your industry and environment, standard racking materials may not be suitable. Ask your shelf racking supplier about custom coatings and material options, such as:
- Rust-Proof Coating – Essential for humid environments like cold storage or outdoor facilities.
- Fire-Resistant Coating – Adds extra protection for warehouses handling flammable materials.
- Heavy-Duty Steel – Reinforced materials for high-load applications.
- Galvanized Coating – Ideal for outdoor or wet environments to prevent corrosion.
- Powder Coating – Provides a durable, smooth finish that resists wear and tear.
- Anti-Microbial Coatings – Useful for food storage or pharmaceutical warehouses.
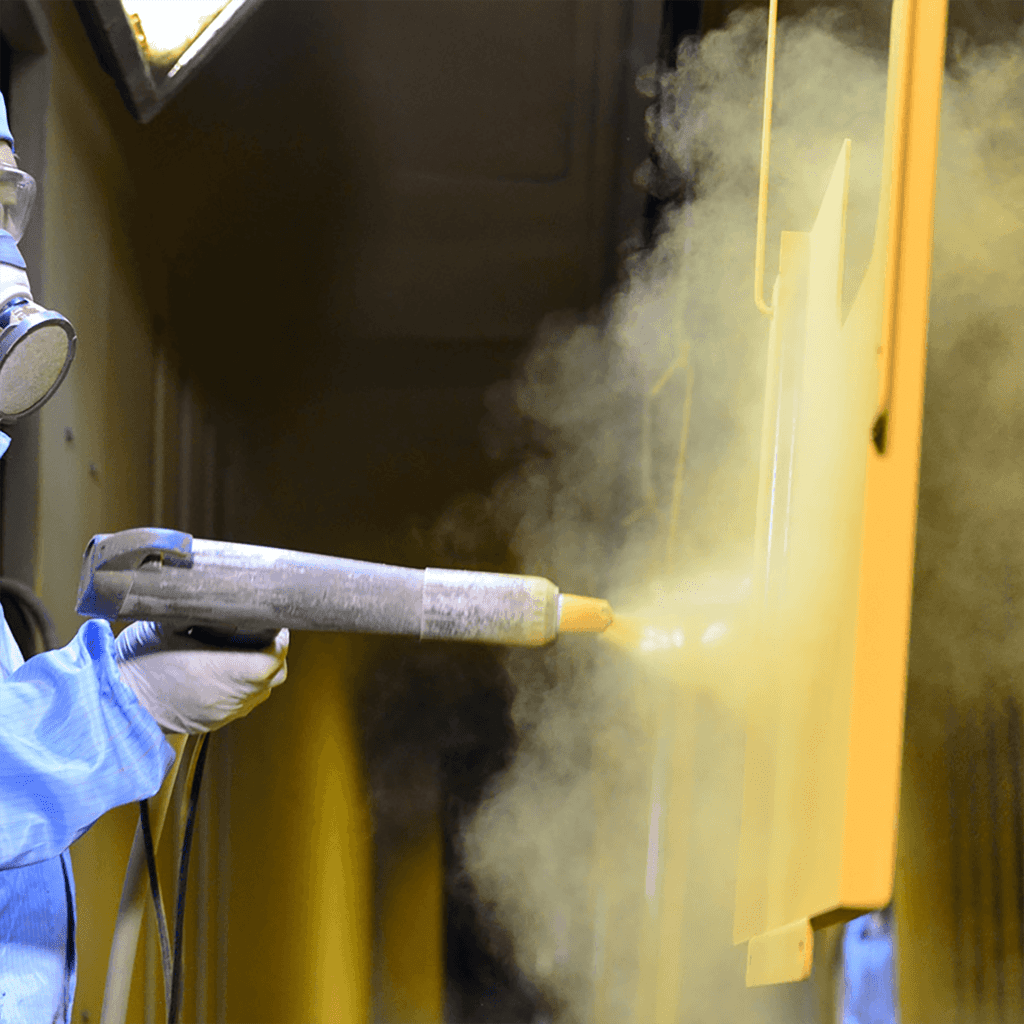
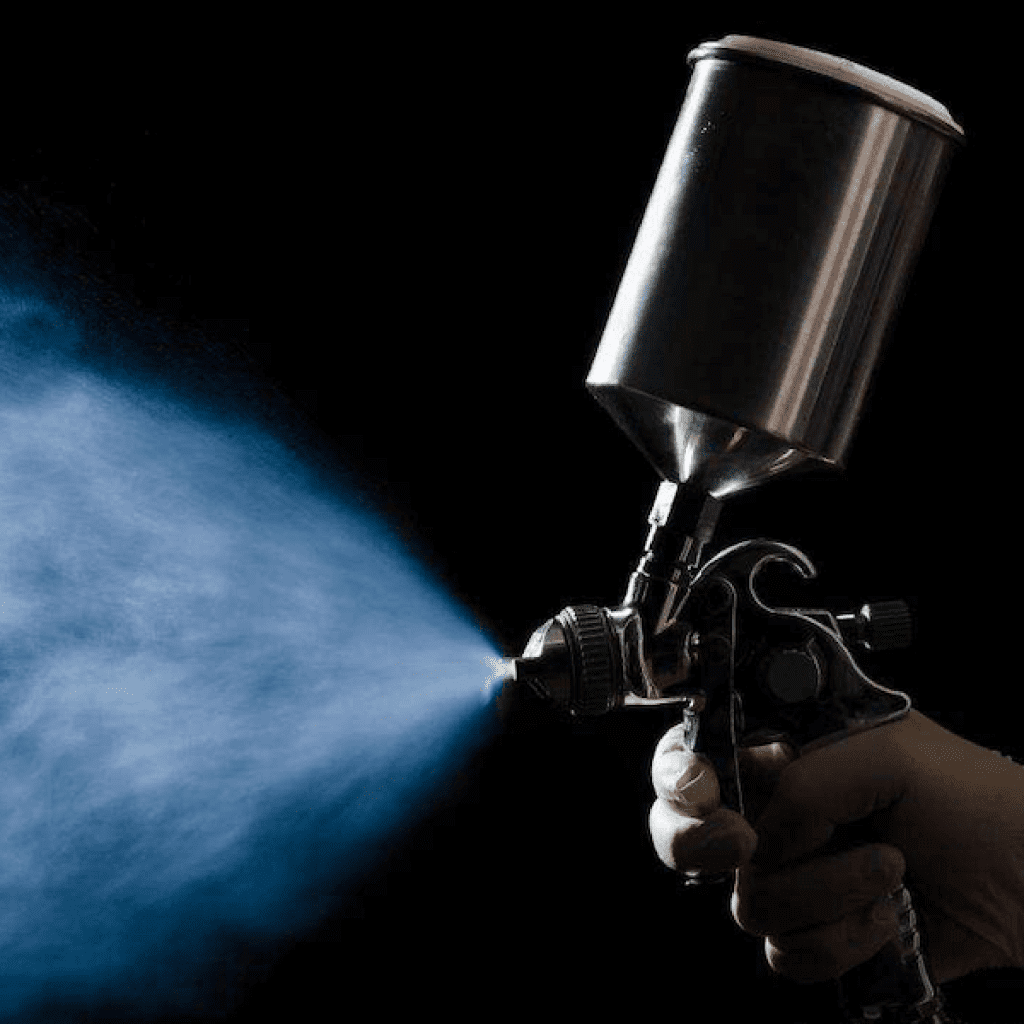
The Cost vs. Benefit of Custom Coatings
A common concern is whether investing in custom coatings is worth the additional cost. However, studies show that rust-resistant coatings can extend rack lifespan by 50%, reducing the need for frequent replacements and saving businesses thousands in long-term costs.
Unsure if you’re getting everything you need?
Don’t risk wasting money on missing add-ons or services. Chat with us today to make sure you’re getting the essential feature and professional services that will truly maximize your warehouse’s potential. Let us guide you in making the best choice for long-term success!
3. Racking Blueprint (Softcopy & Hardcopy) for Storage Optimization
A detailed racking blueprint is crucial for proper warehouse storage planning, placement, upgrades, and future modifications in the long run. Your racking supplier should provide:
- Softcopy (Digital File) – Helps in future adjustments, reconfigurations, and easy sharing with warehouse planners.
- Hardcopy (Printed Plan) – Useful for on-site reference and compliance documentation.
- Customization Options/Profiling – Offers a range of materials and layouts, allowing flexibility both for current needs and future expansion or modifications.
- Load Distribution Plans – Helps prevent uneven weight distribution and ensures rack stability.
- Installation Guidelines – Provides step-by-step instructions for safe and accurate assembly.
Why Digital Blueprints Are Essential for Warehouse Scalability
A study on warehouse efficiency found that businesses with detailed racking blueprints were able to expand operations 30% faster than those without. Having a clear plan reduces downtime and prevents misalignment issues during upgrades.
Must-Have Services from Your Racking Supplier
4. Professional Racking Installation & Compliance Assistance
Racking installation is not just about assembling shelves—it requires proper setup for maximum stability and safety. Straightaway ask if your shelf racking supplier provides:
- Professional Installation Services – Ensures proper anchoring, leveling, and load distribution.
- Safety Compliance Assistance – Verifies that the installation meets local safety regulations and warehouse standards.
- On-Site Supervision – An expert to oversee installation and prevent costly mistakes.
- Post-Installation Inspections – Ensures everything is secure before usage.
Real-World Example: Installation Mistakes That Led to Disaster
In 2019, a major logistics center suffered a catastrophic collapse due to incorrectly installed racks. The total loss amounted to over $2 million. An investigation found that the racks were not anchored correctly, highlighting the importance of professional installation.
5. Preventive Maintenance & Inspections for Storage Racks
Soon, storage racking systems will experience wear and tear, leading to potential failures. Many racking suppliers offer maintenance plans, including:
- Regular Safety Inspections – Identifies early signs of damage or misalignment.
- Replacement of Worn-Out Parts – Prevents unexpected breakdowns.
- Structural Reinforcement Services – Strengthens racks that show signs of weakness.
- Annual Checkups – Ensures compliance with safety regulations.
Why Preventive Maintenance Saves Money
A warehouse that implemented quarterly rack inspections found that rack-related accidents decreased by 60%. Certainly, saving them an estimated $500,000 in damages and liability costs over five years.
Conclusion: Be an Informed Buyer When Choosing a Shelf Racking Supplier
When purchasing a shelf racking system, it’s important to go beyond just the shelves. Asking the right questions can help you secure better safety, efficiency, and long-term savings. From essential racking add-ons like safety accessories and blueprints to installation support, maintenance, and warranties, these factors can make a huge difference in your storage system’s performance.
In summary, by working with a shelf racking supplier that provides complete solutions, not just racks, you can optimize your warehouse storage operations and avoid costly mistakes. Always ask for these additional products and services before making a purchase!
With these key considerations in mind, you can confidently choose the best shelf racking system for your business, ensuring both safety and efficiency in your warehouse storage setup.
Any more questions? Message us directly! Let’s discuss more and get your Free Consultation
How Hyperack Plan Your Racking System?
- Expertise: We dive deep into your warehouse space to determine the best racking configurations tailored to your needs.
- High-Tech Solutions: Our AutoCAD designs maximize storage while ensuring your team has ergonomic access to what they need.
- Side-by-Side Comparisons: Our planning process allows you to compare layout options easily, helping you make informed decisions.
- Data-Driven ROI Calculation: We provide detailed numerical data for each layout, empowering you to understand the impact on your bottom line.
- Customization: Our custom racking systems are built to meet any unique requirements, ensuring the best approach for any facility.
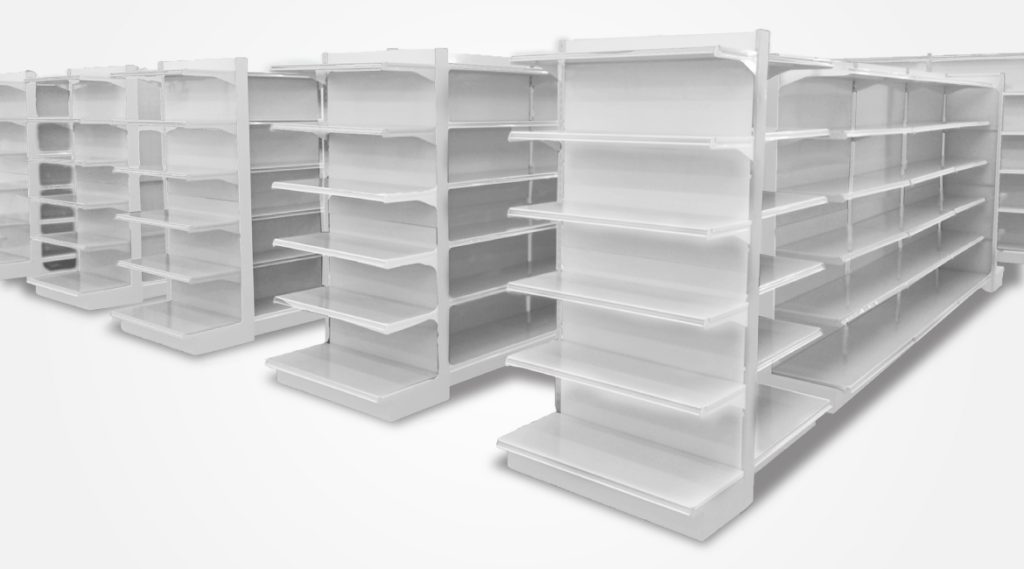
Gondola Rack: Most useful Display Rack in Malaysia
What is a Gondola Rack?
In retail, maximizing product visibility, optimizing floor space, and ensuring long-term durability are crucial for success. One shelving solution that meets all these requirements is the gondola rack, a modular, freestanding system that has become a staple in many retail settings. Whether you’re operating a supermarket, boutique, pharmacy, or electronics store, gondola racks can revolutionize your store layout and boost sales. This comprehensive guide explores what gondola racks are, the technical aspects, types, benefits, and data-backed advantages they bring to retailers.
Definition & Core Features
A gondola display rack is a versatile, freestanding shelving unit used in retail stores to display products in an organized manner. It is designed with adjustable shelves, a sturdy frame, and modular components that allow retailers to customize the setup based on their needs.
The Name “Gondola”
The name “gondola” refers to the rack’s boat-like base, which provides both stability and flexibility. This design ensures that gondola racks are able to withstand the weight of products and heavy foot traffic while being easily reconfigurable to accommodate different store layouts or seasonal displays.
Key Features of Gondola Racks
- Adjustable Shelving
Gondola racks feature adjustable shelves that allow retailers to easily change the height to suit various product sizes. This flexibility is crucial in retail settings where products may vary greatly in height. For example, when stocking a convenience store with snack bags and beverages, the shelving can be adjusted to create a uniform display. - Modular Design
One of the defining features of gondola racks is their modularity. These systems are composed of interchangeable parts that can be easily added or removed based on the needs of the store. According to Retail Solutions magazine, modular gondola racks allow stores to increase product display capacity by up to 30% without cluttering the floor space. - Freestanding Design
Gondola racks are freestanding, meaning they don’t require wall attachments. This is a huge benefit for retailers as it allows them to place these units in high-traffic areas such as aisles, corners, or near entrances. Studies show that freestanding shelving increases shopper engagement by 15% compared to fixed-wall units. - Heavy-Duty Build
Gondola racks are built to handle heavy products. The frames are commonly made from materials such as steel, aluminum, or reinforced plastic. Steel frames, for example, can support up to 500 lbs per shelf, making them suitable for both lightweight and heavyweight items. - Customizable Accessories
Gondola racks come with a range of accessories like hooks, baskets, and sign holders. For example, adjustable hooks allow retailers to display small, hanging items like accessories or bags, while baskets are ideal for products such as cosmetics or small packaged goods. Digital signage can also be added to display promotions or product information, increasing the overall shopper experience and driving sales.
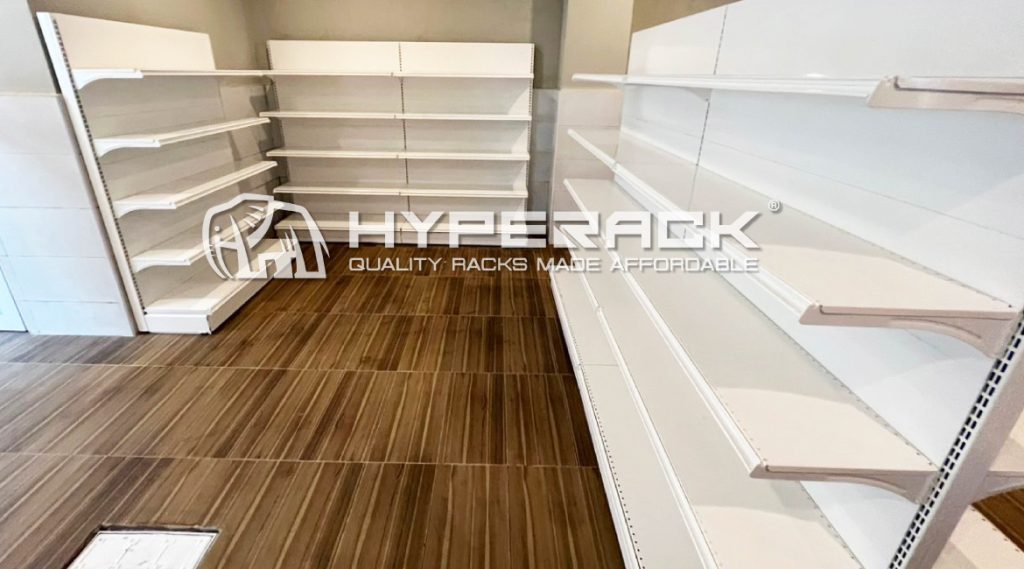
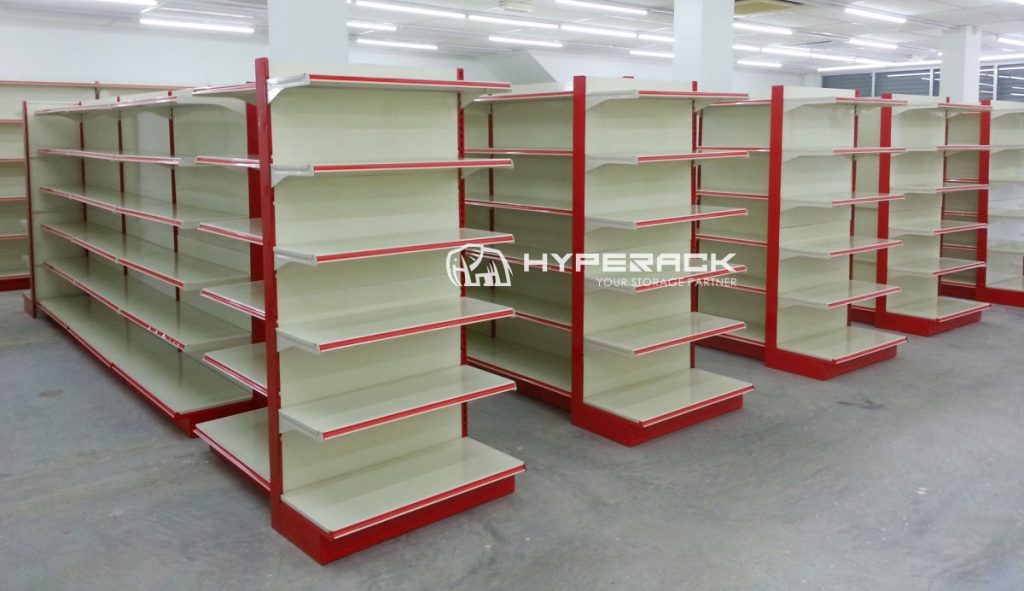
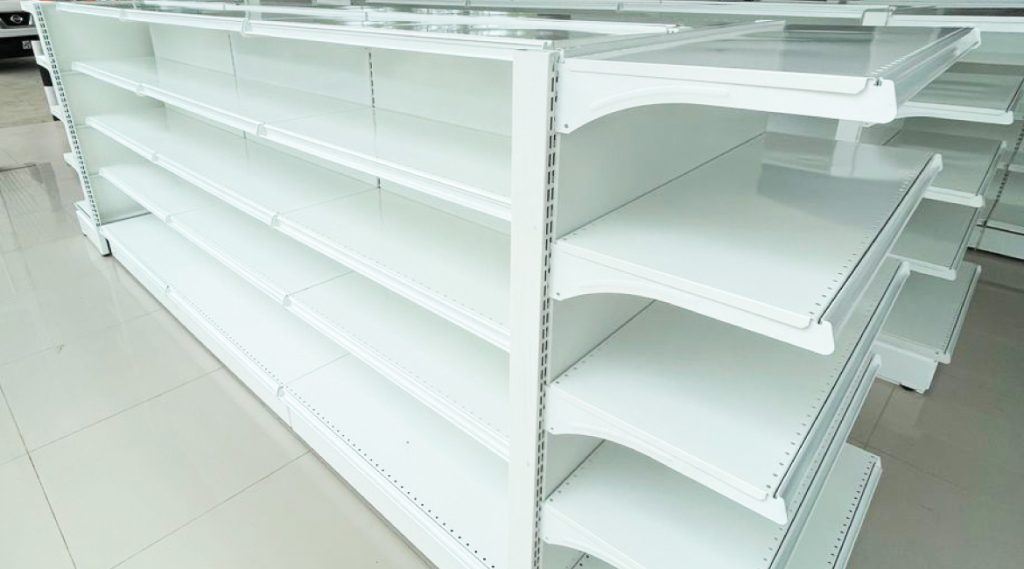
Types of Gondola Racks
Gondola racks are available in several configurations, each designed to meet specific needs. These include:
Single-Sided Gondola Racks
Best for: Wall placements or narrow aisles
Use Case: Single-sided racks are often used along walls or in areas where space is limited. For example, a 7-Eleven convenience store might use single-sided racks to display beverages, snacks, and packaged food. These racks optimize small spaces and can display a variety of products while ensuring easy access for customers.
Double-Sided Gondola Racks
Best for: Central aisles in supermarkets
Use Case: Double-sided design racks are used in the center of aisles to showcase products on both sides. For example, a grocery chain like Tesco may use double-sided gondola racks to display canned goods, dairy products, and beverages. These racks not only maximize the available space but also encourage impulse buying as customers can see products from either direction. According to The Retail Institute, double-sided racks increase product visibility by 20%, leading to higher sales volume.
End Cap Gondola Racks
Best for: High-visibility promotions
Use Case: End cap racks are placed at the end of aisles and are often used to highlight promotional items or seasonal products. A Target store might use end caps to display holiday-themed products, clearance items, or limited-time offers. Studies show that products placed on end caps are 70% more likely to be purchased due to their high visibility.
Corner Gondola Racks
Best for: Maximizing underutilized corners
Use Case: Corner gondola racks are used in small retail spaces to make the most of corner areas. These racks are perfect for stores with limited square footage or for products that benefit from being placed in high-traffic corner spots. For example, a small bookstore may use a corner gondola rack to display books related to a specific genre or author, creating an appealing visual display.
5 Ways Gondola Racks Transform Retail Spaces
1. Space Maximization
Retailers are always looking for ways to maximize their store’s floor space. Retail Gondola racks are designed to optimize vertical space, which is particularly valuable in stores with limited square footage. By increasing the number of product display levels, modern gondola racks can make use of up to 30% more space compared to conventional shelving units. In practical terms, this means that a store can display more products without sacrificing aisle width or creating clutter. A supermarket can use the same floor area to increase product offerings by up to 25% by integrating gondola racks.
2. Enhanced Product Visibility
Product visibility is critical in driving sales. Gondola racks are designed with eye-level displays, which are the most effective way to capture customer attention inside your retail outlets. According to The Nielsen Company, products displayed at eye level see an increase in sales by 20%. By adjusting the height of shelves to suit different product types and placing promotional items at eye level, retailers can enhance product visibility and increase impulse buys.
3. Streamlined Organization
Gondola racks help maintain a clean and organized store layout. Products can be categorized by type, price, or brand, making it easier for customers to find what they are looking for. Studies show that organized stores see an increase in customer satisfaction by 25%, as shoppers can find their desired items faster. This streamlined organization not only improves the shopping experience but can lead to higher conversion rates.
4. Layout Flexibility
The modular nature of gondola racks allows for rapid changes in store layouts. Retailers can easily reconfigure the arrangement of racks based on seasonal promotions, special sales, or new inventory. For instance, during Black Friday, a store can easily adjust its gondola racks to display holiday-themed items or discounted products in prime locations, maximizing foot traffic and sales.
5. Durability = Cost Savings
Investing in high-quality gondola racks reduces long-term costs associated with store maintenance. Steel or custom gondola rack, in particular, can last for decades due to their robust construction. As a result, stores spend less on replacements and repairs. According to Retailer’s Journal, stores that invest in quality gondola racks experience a 30% reduction in replacement costs over a 5-year period compared to stores that use lower-quality shelving systems.
Strategies to Leverage Gondola Racks for Influencing Purchase Intention
While gondola shelving system are versatile and functional, retailers can implement additional strategies to further leverage their potential to influence purchase intention and enhance the shopper experience:
- Strategic Product Placement:
Position high-margin or impulse-buy products at eye level on gondola racks. Products that are easy to grab and quick to purchase, such as snacks, drinks, or beauty products, should be placed in prime positions to encourage spontaneous buys. Research by Journal of Retailing indicates that products placed at eye level experience up to 50% higher sales compared to those on lower shelves. - Seasonal Displays & Promotions:
Adjust gondola rack configurations during key retail periods such as holidays, back-to-school, or seasonal sales. For example, displaying commercial summer-themed items like sunscreen and beach towels on gondola racks during peak shopping periods not only attracts attention but aligns with shoppers’ needs at that time. Harvard Business Review found that seasonal displays can boost sales by 30-40% when strategically placed on gondola racks. - Incorporating Digital Signage:
Add digital screens or interactive signage to gondola racks to engage customers further. This could be used to display promotions, product features, or reviews. Digital signage has been shown to increase customer engagement and impulse purchases by 20%, driving more sales and influencing purchase decisions. - Encouraging Cross-Selling with Accessories:
Gondola racks are excellent for cross-selling complementary products. For example, if a store sells shoes, gondola racks can display socks, shoe polish, or laces alongside the footwear. This strategy not only increases the overall sales volume but also improves the customers’ experience by offering related products in an organized manner. - Creating Themed Zones:
Use gondola racks to create product zones based on specific themes, such as “Health & Wellness” or “Back-to-School Essentials.” This can influence shopper decisions by grouping related items together, making it visually appealing and easier for customers to find what they’re looking for. According to Marketing Science, shoppers are 10% more likely to purchase additional items from themed sections.
Industry Applications: Where Gondola Racks Shine
Gondola racks are used across a range of industries, each benefiting from the versatility and durability of the system:
- Supermarkets / Hypermarket: Gondola racks are ideal for displaying bulk items, snacks, beverages, and canned goods. Their customizable design allows for different configurations depending on the store’s needs.
- Pharmacies: Organize over-the-counter medications, vitamins, and personal care products efficiently. The ability to adjust shelf heights ensures that products of varying sizes can be displayed.
- Electronics Stores: Gondola racks are perfect for securely displaying gadgets, chargers, and accessories. Their heavy-duty construction allows them to hold heavier items like televisions or home appliances.
- Apparel Stores: Display folded clothes, shoes, or accessories. Gondola racks with hooks can also accommodate hanging items like belts, scarves, and bags.
- Bookstores: Gondola racks are effective for displaying bestsellers, new arrivals, or theme-based collections. Their adjustable shelves make them versatile for various book sizes.
FAQs: Gondola Racks Demystified
- Q: How much weight can a gondola rack hold?
A: Steel gondola racks typically hold up to 500 lbs per shelf, but the exact weight capacity can vary depending on the manufacturer’s specifications. - Q: Are gondola racks easy to assemble?
A: Yes, most gondola racks Malaysia are designed for easy, tool-free assembly. Modular components are quick to set up, making them ideal for retailers who frequently change their store layout. - Q: Can gondola racks be used outdoors?
A: Yes, gondola racks can be used outdoors. Be sure to choose weather-resistant materials like coated steel or aluminum to ensure they hold up against the elements.
Conclusion: Elevate Your Retail Strategy with Gondola Racks
Gondola racks are not just practical; they are a game-changer for retailers looking to improve product displays, optimize space, and drive sales. With their adjustable shelving, modular design, and customizable features, gondola racks are an investment that pays off over time. By providing enhanced product visibility, increasing customer engagement, and maximizing floor space, these racks help retailers create a more dynamic and efficient shopping environment.
Investing in gondola racks is a strategic move that can help elevate your retail store’s operations and transform your shopping experience. Looking for a good Gondola rack supplier Malaysia is important too.
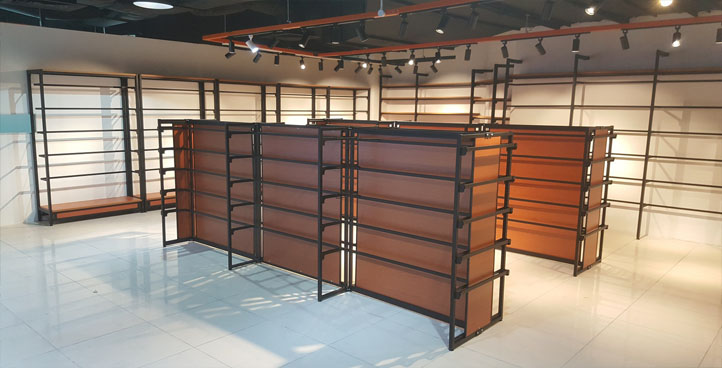
What is OPPA Racks? : A Comprehensive Guide
Maximizing Retail Efficiency with OPPA Racks: A Comprehensive Guide
In retail world, including Malaysia, creating an environment that’s both attractive and functional is essential for success. With so many products to display and a limited amount of space, retailers often face the challenge of balancing product visibility with efficient use of available space. Enter the OPPA rack—a modern and versatile display and storage solution that is revolutionizing the way retail spaces are designed.
As retail stores evolve to meet the needs of a changing consumer landscape, OPPA racks have gained popularity due to their ability to offer more than just storage. With a blend of style, flexibility, and practicality, OPPA racks are ideal for businesses looking to create a seamless shopping experience while maximizing the potential of their storage systems.
In this article, we will explore the benefits, features, and implementation of OPPA racks in retail spaces. We will also delve into how these racks can transform your store layout and help you achieve a more organized and efficient space. Whether you own a boutique, a supermarket, or a large retail store in Malaysia, this guide will provide valuable insights into how to incorporate OPPA racks into your storage system.
What Are OPPA Racks?
OPPA racks are a type of display rack that combines the aesthetic appeal of modern design with the functionality of a storage system. They are popular in retail stores due to their versatile configurations, allowing for efficient product display and easy access for customers. The term “OPPA” is inspired by Korean culture, and as such, these racks often feature sleek, minimalist designs that complement a wide range of retail environments.
While OPPA racks are widely used in various retail spaces, they are not limited to traditional warehouse settings. Unlike heavy-duty industrial racks, OPPA racks focus on visual appeal and ease of access, making them ideal for smaller or mid-sized retail stores, boutiques, and even malls.
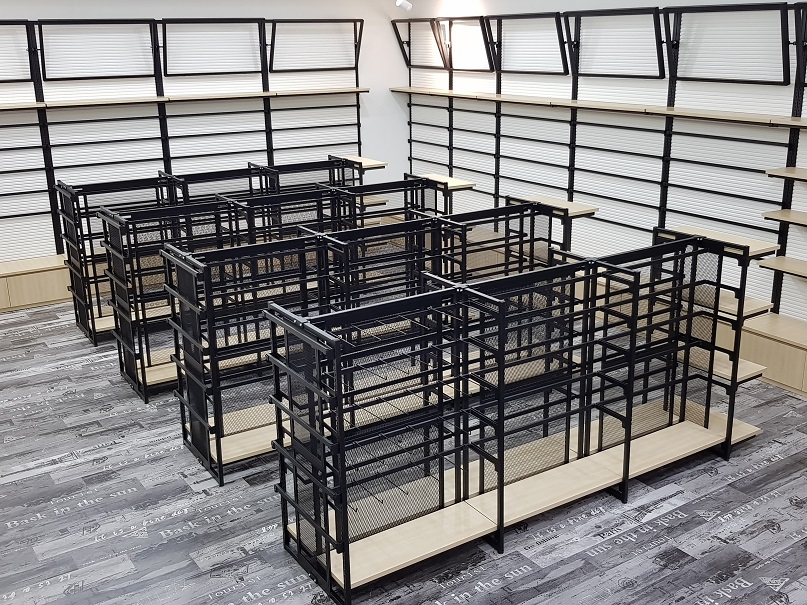
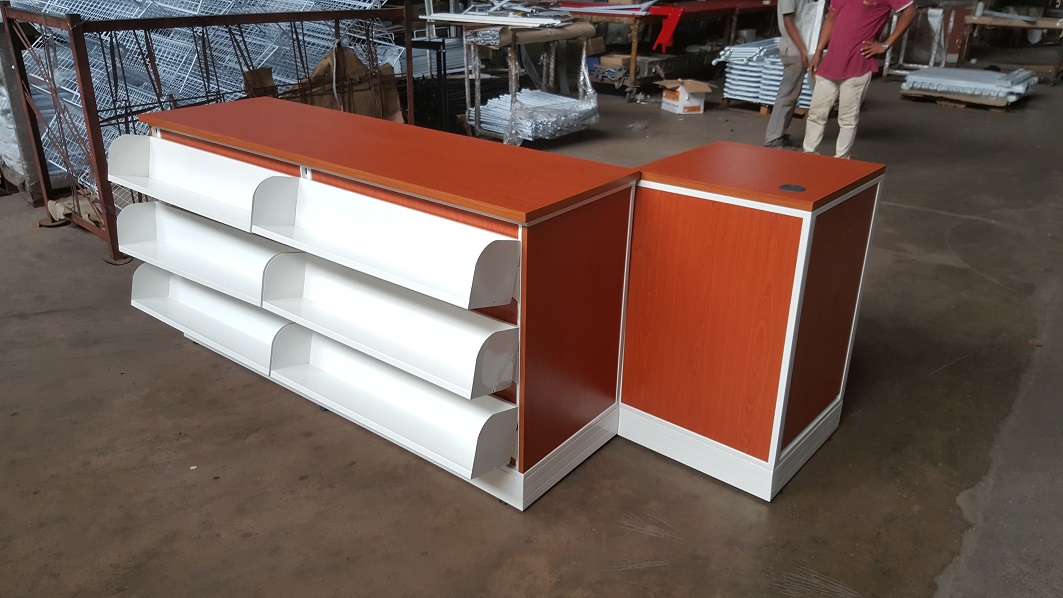
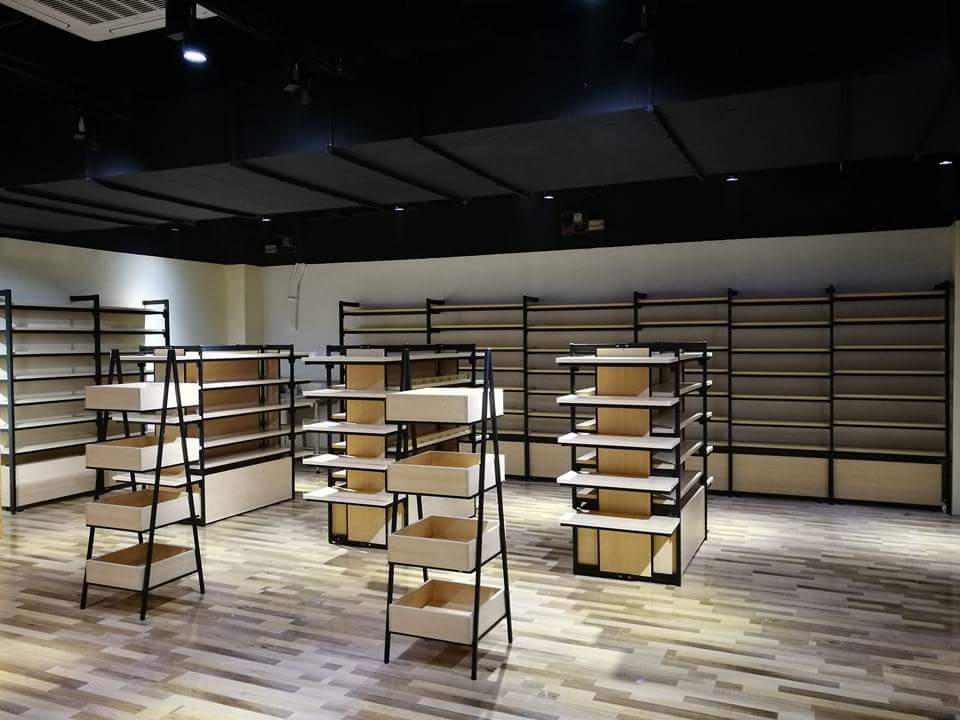
Key Features of OPPA Racks
Modern Design
OPPA racks stand out due to their sleek, clean lines and contemporary design. These racks are influenced by modern Korean aesthetics, which emphasize simplicity and elegance. Whether your store has a minimalist, industrial, or more eclectic design, OPPA racks can seamlessly integrate into your layout.
Versatility
OPPA racks are available in a wide range of configurations, including single-tier and multi-tiered designs, wall-mounted units, freestanding shelves, and adjustable stands. This variety allows retailers to choose a setup that best suits their specific needs, whether they’re displaying clothing, accessories, shoes, or even small electronics.
Durability
Despite their lightweight appearance, OPPA racks are constructed from durable materials like metal, wood, or high-quality plastic. This ensures that they can withstand the daily wear and tear of a busy retail environment, handling everything from clothing racks to heavier product displays.
Spaces
A standout feature of OPPA racks is their ability to optimize the storage and display of products. They help you maximize the use of your retail space without sacrificing accessibility. Whether you’re dealing with small, delicate items or larger pieces, OPPA racks are designed to store products in an organized, easily accessible manner, improving both the customer experience and internal workflow.
Is Your Store Ready for a Serious Upgrade?
Stop cramming products into every corner! OPPA racks are built to organize, showcase, and elevate your retail game. Let’s talk and get your store looking sharp and efficient—contact us now to make the change!
Why OPPA Racks are Ideal for Retail Stores in Malaysia
In Malaysia’s competitive retail market, standing out is crucial for driving sales and improving customer satisfaction. One way to achieve this is by creating an organized, aesthetically pleasing store layout. OPPA racks provide the perfect blend of both. Here are some reasons why OPPA racks are ideal for retail stores in Malaysia:
Enhanced Product Display
With their open and stylish design, OPPA racks offer better product visibility. Customers can easily view and interact with the products on display, increasing the likelihood of impulse buys. Moreover, the clean design ensures that products are showcased in a visually appealing manner, attracting more foot traffic into the store.
Maximized Storage Space
Retail space can be limited, especially in urban areas like Kuala Lumpur, Johor Bahru, and Penang, where square footage is often at a premium. OPPA racks help retailers make the most of every inch of available space by utilizing vertical storage options. By stacking products or displaying them in multi-tiered units, these racks ensure that retailers can store more without taking up additional floor space.
Flexible Configurations
OPPA racks can be customized to fit various store layouts and sizes. Whether you need a compact wall-mounted unit for a small store or a large freestanding display for a department store, OPPA racks can be adapted to suit your specific needs. This flexibility makes them suitable for businesses of all sizes, from local boutiques to large retail chains.
Improved Store Aesthetics
The clean, modern design of OPPA racks adds a touch of sophistication to any retail space. They can complement a variety of store themes, whether you’re operating in a trendy mall in the heart of Kuala Lumpur or a cozy boutique in the suburbs of Penang. The ability to create a visually appealing shopping environment is crucial in attracting customers and building brand loyalty.
Easy Maintenance
One of the biggest advantages of OPPA racks is their ease of maintenance. Unlike traditional racking systems that may require frequent inspections or maintenance, OPPA racks are built with materials that are resistant to corrosion and wear. This reduces the time and money spent on upkeep, allowing you to focus more on growing your business.
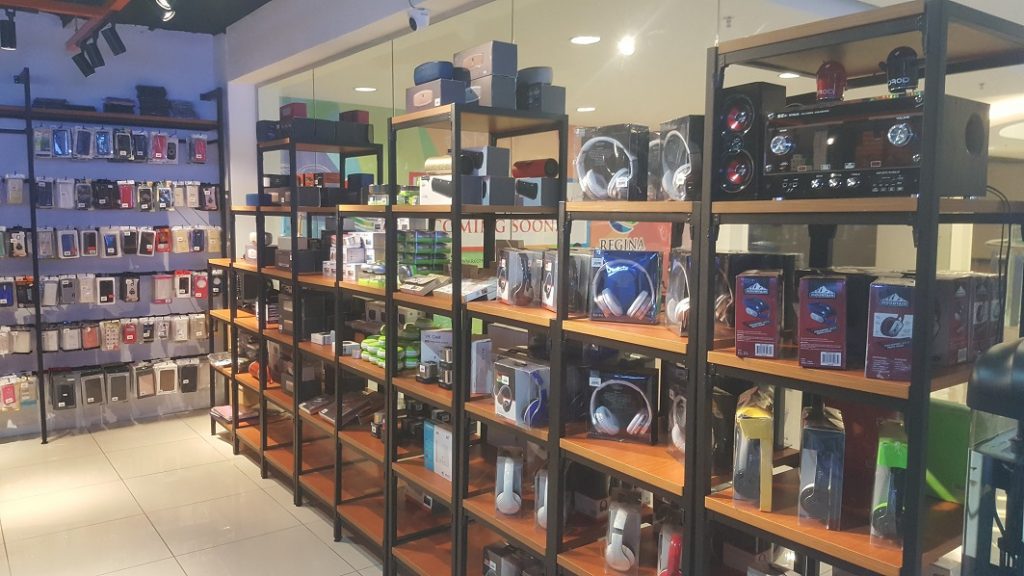
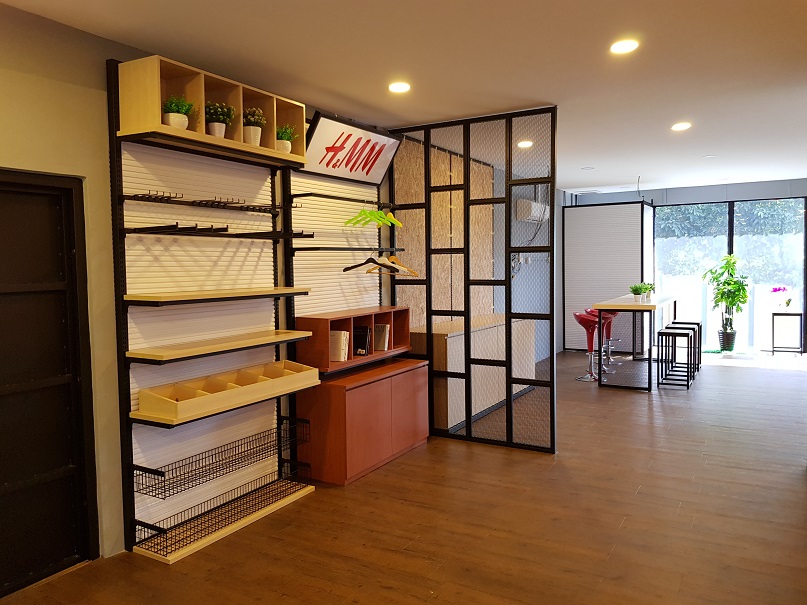
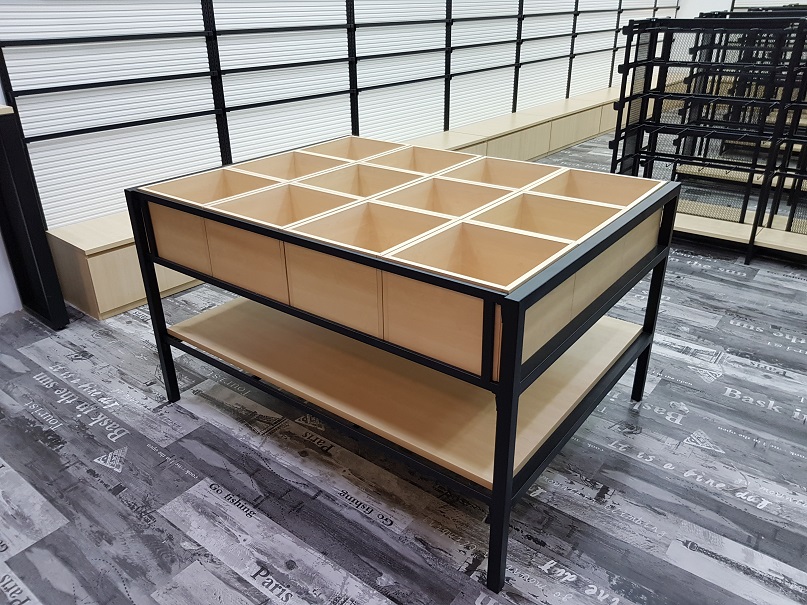
How to Incorporate OPPA Racks into Your Store
Assess Your Store’s Layout
Before selecting OPPA racks, it’s important to assess your current store layout. Consider the flow of foot traffic, available space, and the types of products you sell. For example, if you have a lot of small items, wall-mounted OPPA racks can help display them neatly. For larger products, consider using freestanding racks or multi-tiered units to optimize space while keeping everything within easy reach.
Choose the Right Type of OPPA Rack
There are various types of OPPA racks to choose from, each with different features and configurations. Some popular options include:
- Wall-Mounted Racks: Ideal for smaller retail spaces, wall-mounted racks help maximize vertical space and provide a clean, minimalistic look.
- Freestanding Units: These are versatile and can be placed anywhere in the store. They’re perfect for creating focal points or for showcasing new or promotional products.
- Multi-Tiered Shelves: These racks provide additional space for storing products and are ideal for retailers with a high volume of inventory.
Plan for Flexibility
Retail businesses are dynamic, and your storage and display needs may change over time. Choose OPPA racks that offer flexibility and adaptability. Modular designs are a great option, as they can be reconfigured to suit different products or layouts as your store evolves.
Collaborate with Suppliers
Once you’ve assessed your needs and chosen the right type of OPPA rack, it’s time to partner with a supplier. In Malaysia, there are several reputable suppliers of OPPA racks, including local businesses that specialize in storage solutions. Make sure to work with a supplier that understands your specific needs and can provide tailored solutions.
Where to Find OPPA Racks in Malaysia
Several suppliers in Malaysia offer OPPA racks designed for retail environments. Here are a few notable ones:
- Hyperack (Klang, Malaysia) – A leading supplier of storage and racking systems, offering a range of OPPA racks suitable for different retail applications. Check Here
- Yepe Sdn Bhd (Kuala Lumpur, Malaysia) – Specializes in Korean-inspired racking solutions, including OPPA racks for retail spaces.
- Y3 Display & Storage System (M) Sdn Bhd (Johor Bahru, Malaysia) – Offers modular racking systems, including customizable OPPA racks.
These suppliers can help you find the right OPPA racks that align with your business needs and retail objectives.
Conclusion
OPPA racks represent a smart and stylish solution for retailers looking to improve their store layout, display products effectively, and maximize storage space. With their versatility, durability, and sleek design, OPPA racks are ideal for retail stores in Malaysia, from boutiques to larger retail chains.
By carefully selecting the right type of OPPA rack, working with trusted suppliers, and integrating these racks into your store layout, you can create a more organized, aesthetically pleasing, and efficient shopping environment. Whether you’re looking to increase sales, enhance customer experience, or optimize your storage system, OPPA racks are an investment that will help your retail business grow and thrive in a competitive market.
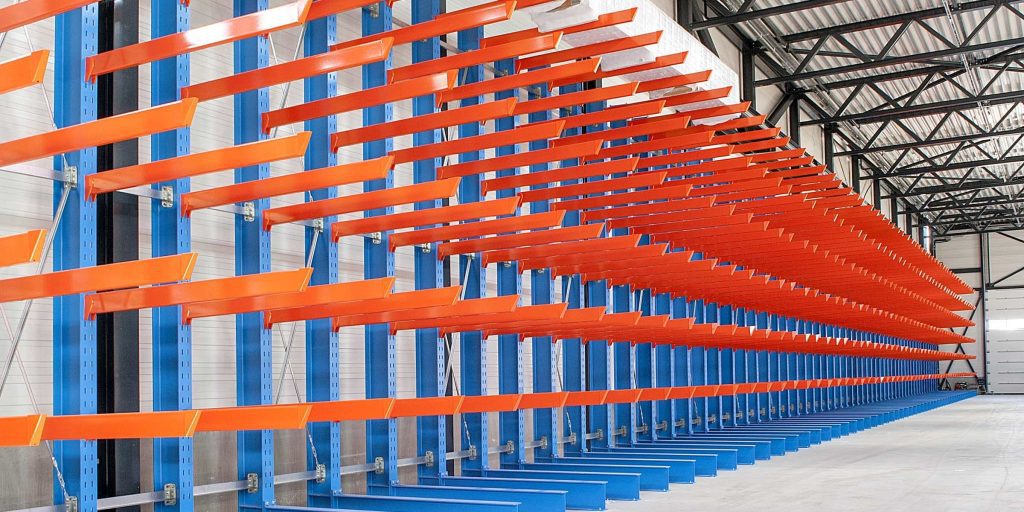
What is Cantilever Racking?
Cantilever Rack System: What You Need to Know
If you’re in the world of warehousing or material handling, you’ve probably heard the term “cantilever racking” tossed around quite a bit. But what exactly is cantilever racking, and why should you care about its advantages in an outdoor or industrial setting? This article dives deep into the cantilever rack system, exploring how it works, its many advantages, and why it might just be the perfect storage solution for your bulky items, including steel bar stock. So grab a seat and let’s unpack everything you need to know about this versatile storage system.
What is a Cantilever Rack and How Does it Work?
Understanding the Cantilever Rack System
A cantilever rack is a specialized storage system designed to handle items that are too bulky or awkward for conventional racking systems. Unlike traditional pallet racks that have vertical beams, cantilever racks feature horizontal arms that extend outward from a vertical upright, creating a unique design that allows for easy access and storage of long or heavy items. This system allows for both single-sided and double-sided configurations, making it perfect for warehouses where space is a premium.
Key Components of Cantilever Racking
The cantilever rack system is made up of a few key components, including the upright supports, cantilever arms, and shelves. The uprights are typically made of heavy-duty steel, which provides the strength and durability needed to support substantial loads. The cantilever arms are adjustable, allowing you to customize the height and spacing based on your storage needs. This flexibility is one of the standout features of the cantilever storage system, making it suitable for a wide range of materials, from metal pipes to plywood sheets.
How Cantilever Racking Works for Bulky Items
When it comes to storing bulky items, the cantilever rack system shines. The design allows for easy loading and unloading, which is crucial for medium duty and heavy-duty storage solutions, especially when dealing with industrial materials. You can easily store and retrieve products without having to navigate around cumbersome beams. Imagine needing to store large, heavy materials like steel beams or long pipes; with a cantilever rack, you can simply slide the items onto the cantilever arms, and voilà, they’re securely stored in a way that maximizes your warehouse space.
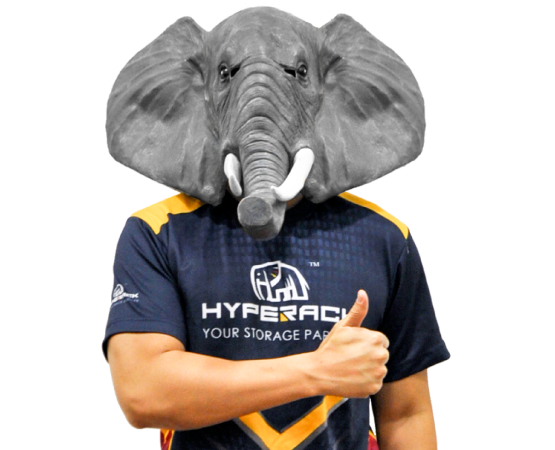
Ask us anything about Cantilever Racking!
Talk to us for a FREE CONSULTATION! Whether you’re unsure about sizing, load capacity, or setup, we’ll walk you through everything step by step and help you find the best solution for your storage needs.
What are the Advantages of Cantilever Racking?
Space Optimization in Warehouses
One of the primary advantages of cantilever racking is its ability to optimize warehouse space, especially when dealing with long-length items like steel bar stock. With its vertical storage design, you can utilize height for storage, which is often underused in many warehouses. Instead of wasting valuable floor space, a cantilever rack system allows you to stack items vertically while maintaining easy access. This is especially important in warehouses where every square foot counts, as it enables you to store more within a smaller footprint.
Versatility for Different Material Types
Cantilever racking is incredibly versatile, making it suitable for various material types. Whether you’re dealing with light duty items like small boxes or extra heavy duty cantilever racks for massive steel girders, this industrial system can handle it all. The adjustable cantilever rack arms mean you can easily adapt your storage solution as your inventory changes, making it a practical choice for industries that require flexibility in their storage designs. You can choose for the single sided arm or a double sided arm
Heavy Duty Storage Solutions
For those in need of heavy-duty storage solutions, cantilever racking is often the answer. The robust design, typically made from steel, allows these racks to support a significant amount of weight per arm, making them ideal for storing steel bar stock. This means you can store heavier items without worrying about the structural integrity of your storage system. Plus, this kind of storage rack capacity can be tailored to meet your specific storage requirements, ensuring safety and efficiency in your warehouse operations.
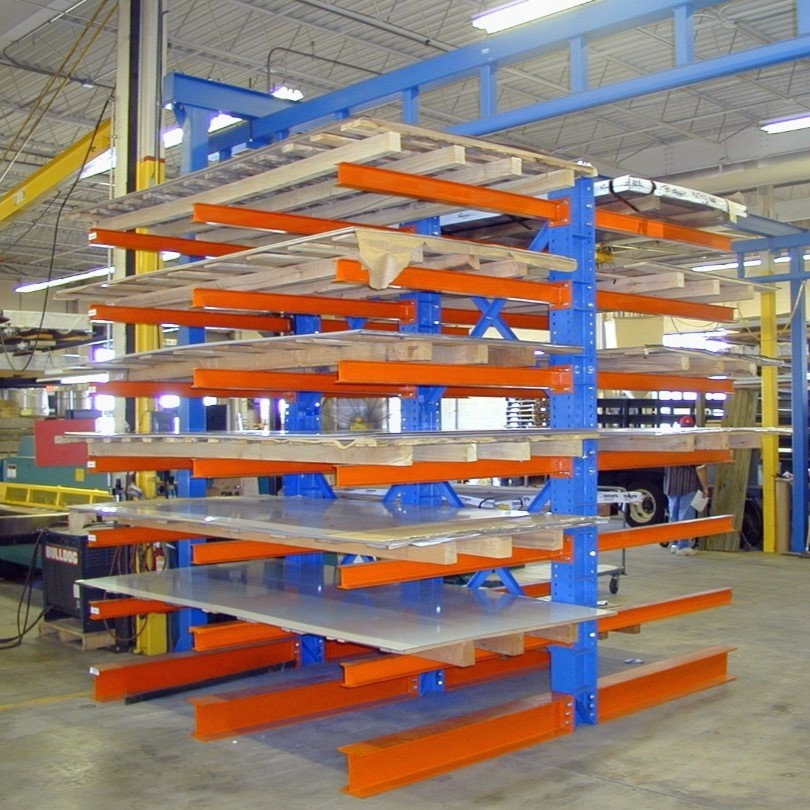
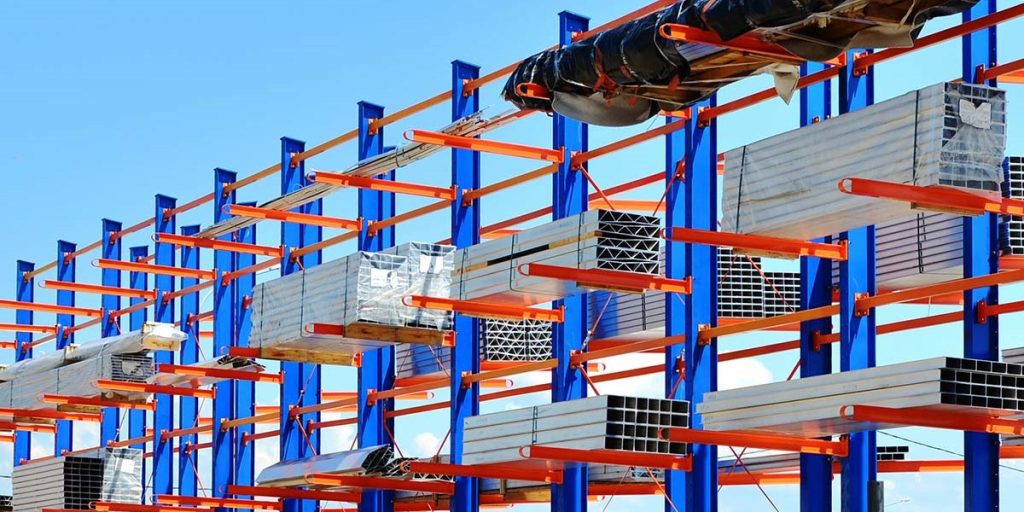
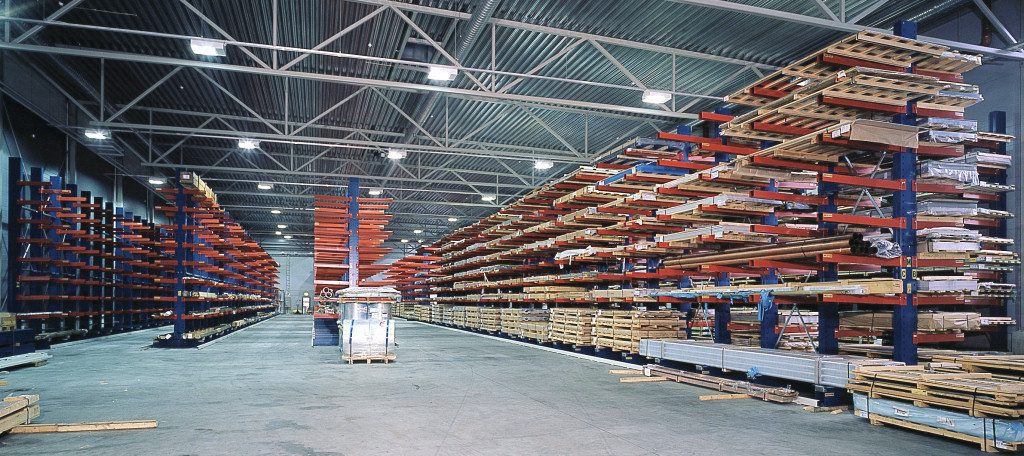
When Do You Need a Cantilever Rack System?
Identifying Storage Needs for Bulky Items
Determining whether you need a cantilever system often comes down to identifying your storage needs for bulky items. If your inventory includes large or irregularly shaped materials, then a cantilever rack is likely the best choice. These racks are particularly useful in industries like construction, manufacturing, and retail, where storing large products is a daily challenge. If you find yourself constantly battling clutter and disorganization due to your bulky items, it’s time to consider implementing a cantilever rack.
Assessing Warehouse Space Requirements
Before you dive into purchasing a cantilever rack system, you’ll want to assess your warehouse space requirements. Consider the layout of your warehouse and how much vertical space you can utilize. A cantilever rack capacity can dramatically change the way you use your space, but it’s essential to ensure that you have the right dimensions and clearance for your items. Working with a supplier or manufacturer who specializes in cantilever pallet racking can help you design a storage solution that fits perfectly in your warehouse.
Cost Considerations for Implementing a Cantilever Rack
When it comes to the price of implementing a cantilever rack system, it’s important to consider both the initial investment and the long-term savings it can provide. While the upfront cost might seem significant, the efficiency gained in material handling and storage organization can lead to reduced operational costs over time, especially in an industrial setting. Additionally, the durability of steel cantilever racks means they are built to last, so you won’t be facing constant replacement costs, making them a worthwhile investment for any warehouse.
What Materials are Used in Cantilever Racking?
Common Materials for Cantilever Rack Construction
The most common materials used in cantilever rack construction are metal, specifically steel. This choice of material ensures the strength and durability needed to handle heavy loads. Some manufacturers may also offer options in lighter materials for light duty applications, but for heavy duty storage solutions, steel is the way to go. It’s vital to choose the right material based on the size and capacity of the items you plan to store, especially if you need cantilever rack for heavier loads.
Benefits of Steel in Cantilever Storage Systems
Steel offers numerous benefits in cantilever storage systems, including resistance to bending and deformation. This means cantilever racking is ideal that even under heavy loads, your cantilever arms and uprights will maintain their structural integrity. Furthermore, steel is relatively low maintenance, which means you won’t have to worry about rust or wear and tear as often as you might with other materials. If you’re looking for a long-lasting solution for your warehouse, steel cantilever racks are a smart choice.
Choosing the Right Material for Your Needs
When choosing the right material for your cantilever racking, think about the specific needs of your warehouse and how they require your system to perform. If you’re storing lightweight items, you might consider lighter materials or even a medium-duty rack. However, if your inventory consists of heavy or bulky items, investing in heavy-duty steel cantilever racks is essential. Assess your storage needs carefully, and don’t hesitate to consult with suppliers to find the perfect material for your cantilever storage system.
Are There Case Studies on Successful Cantilever Rack Implementations?
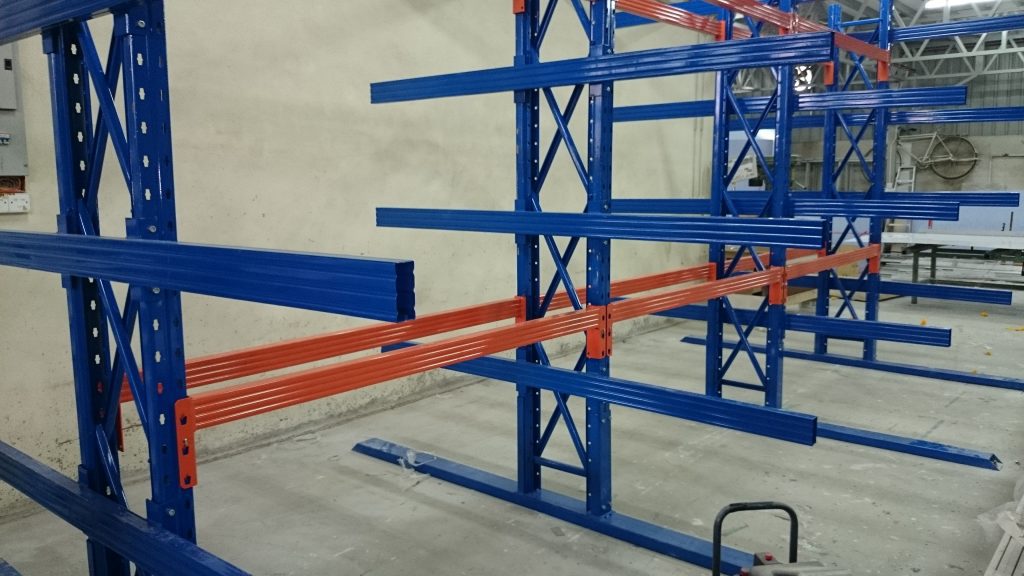
Real-World Examples of Cantilever Racking
There are plenty of real-world examples showcasing the effectiveness of cantilever racking. For instance, Hyperack client in Cheras Selangor a large event company was able to significantly improve its material handling operations by implementing a cantilever rack system for its huge event material and prep. They found that not only did they save space, but they also reduced the amount of time required to retrieve materials for projects involving long-length items. This kind of success story is common among businesses that switch to a cantilever storage solution.
Lessons Learned from Cantilever Rack Systems
One of the key lessons learned from various implementations is the importance of proper planning. Companies that took the time to assess their specific storage needs and tailor their cantilever racks accordingly experienced much greater success than those who opted for a generic solution. Customization in size and capacity is crucial to ensure that the cantilever rack system works effectively within your warehouse layout.
Evaluating the Effectiveness of Storage Solutions
Lastly, evaluating the effectiveness of your cantilever rack system is vital for ongoing success, particularly in industries that require you to retrieve products with varying weights. Regular assessments can help identify any needed adjustments or expansions as your inventory changes. By keeping track of how well your racks are serving your storage needs, you can make informed decisions about future purchases or modifications. In the world of warehousing, staying agile and responsive to your storage solutions is key to maintaining efficiency and productivity.
Conclusion
The cantilever rack system offers a flexible and efficient storage solution for warehouses dealing with bulky or long items. Its design enhances space utilization, accessibility, and adaptability, making it a valuable asset in optimizing warehouse operations.
How Hyperack Plan Your Racking System?
- Expertise: We dive deep into your warehouse space to determine the best racking configurations tailored to your needs.
- High-Tech Solutions: Our AutoCAD designs maximize storage while ensuring your team has ergonomic access to what they need.
- Side-by-Side Comparisons: Our planning process allows you to compare layout options easily, helping you make informed decisions.
- Data-Driven ROI Calculation: We provide detailed numerical data for each layout, empowering you to understand the impact on your bottom line.
- Customization: Our custom racking systems are built to meet any unique requirements, ensuring the best approach for any facility.
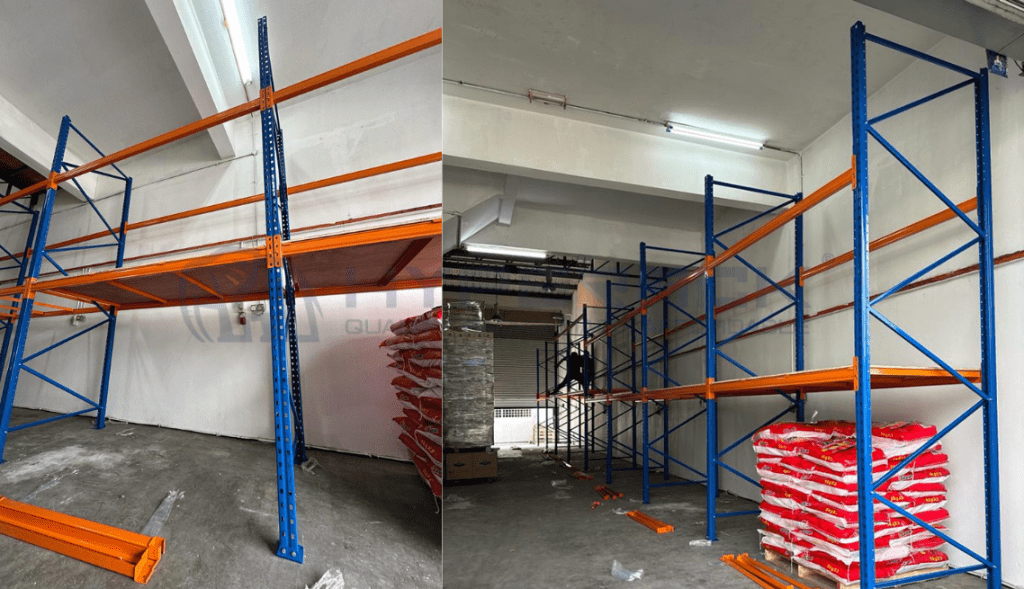
What is Medium & Heavy-Duty Racking?
Medium/Heavy Duty Racking
If you manage a warehouse, factory, or storage facility, you’ve likely faced the challenge of organizing heavy goods efficiently. Limited space and improper storage solutions can lead to disorganization, inefficiency, and even safety hazards.
Medium and heavy-duty racking is one of the racking types that plays a crucial role.
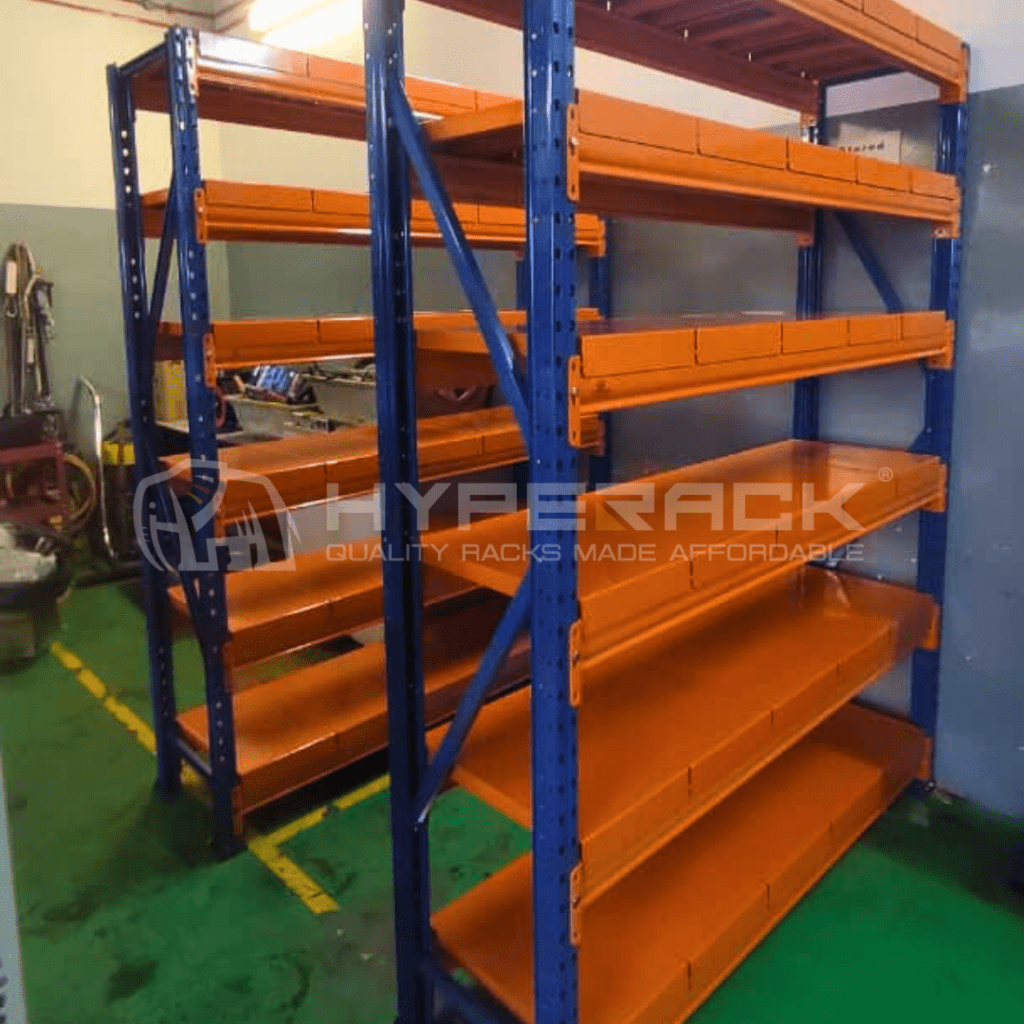
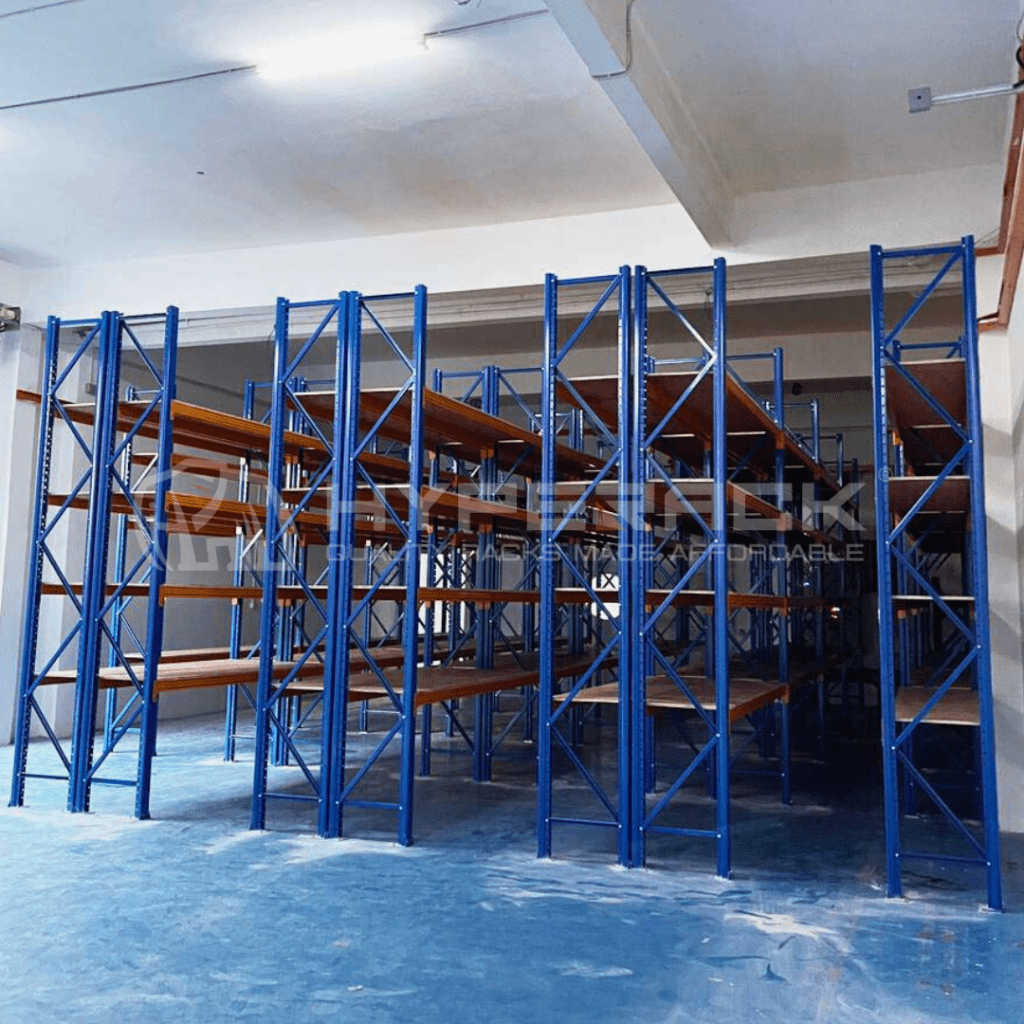
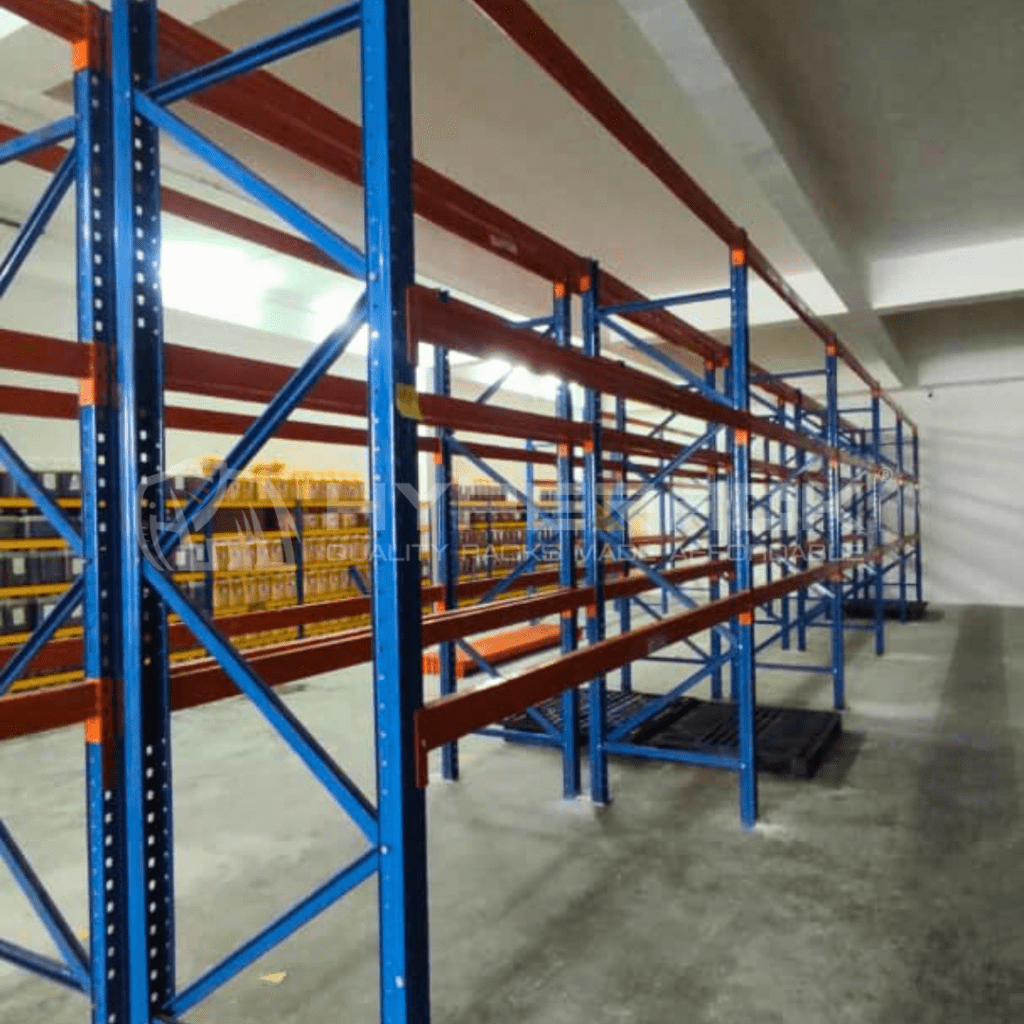
The different Between Medium/Heavy Duty Racking with other types or racking
To choose the right racking system, it’s important to understand the four main categories:
- Light Duty Racking – Holds up to 200kg per shelf and is commonly used for light storage in offices, retail, and homes.
- Medium & Heavy-Duty Racking – Supports 500kg to 4000kg per shelf, providing a balance of strength and flexibility for various industries.
- Racking Systems – Includes specialized solutions like pallet racking and ASRS (Automated Storage and Retrieval Systems) designed for high-volume storage.
- Racking Supported Platform – Multi-level storage designed to maximize vertical space and create additional workspace.
For most businesses dealing with industrial materials, medium and heavy-duty racking is a practical and reliable choice.
Medium-Duty Racking: A Versatile Storage Option
Medium-duty racking provides a structured and simple storage system for businesses that require more strength than traditional shelving but don’t need the full capacity of heavy-duty racking.
Key Features of Medium-Duty Racking:
✔️ Holds Up to 500kg Per Shelf – Suitable for moderate industrial storage.
✔️ Modular & Adjustable Design – Allows for customization and expansion.
✔️ Durability & Corrosion Resistance – Ensures a longer lifespan.
✔️ Efficient Space Utilization – Optimizes storage while maintaining accessibility.
Common Applications:
✅ Storing cartons, boxes, and industrial components
✅ Keeping tools and equipment well-organized
✅ Managing raw materials and finished goods
This type of racking is ideal for businesses that require simplicity and scalability in their storage systems.
Heavy-Duty Racking: Built for Strength and Stability
For industries handling heavy-weight materials and bulk storage, heavy-duty racking offers a secure and high-capacity solution.
Key Features of Heavy-Duty Racking:
✔️ Supports Up to 4000kg Per Shelf – Designed for substantial loads.
✔️ High-Strength Steel Construction – Ensures durability and stability.
✔️ Enhanced Safety Features – Prevents rack failures and workplace accidents.
✔️ Maximizes Vertical Storage – Allows better use of warehouse height without expanding the floor area.
Common Applications:
✅ Palletized goods in warehouses and distribution centers
✅ Heavy machinery parts and automotive components
✅ Large and bulky raw materials for manufacturing
Heavy-duty racking is particularly useful in environments with Simple movement and Heavy-scale inventory storage.
What Makes Medium & Heavy-Duty Racking Special?
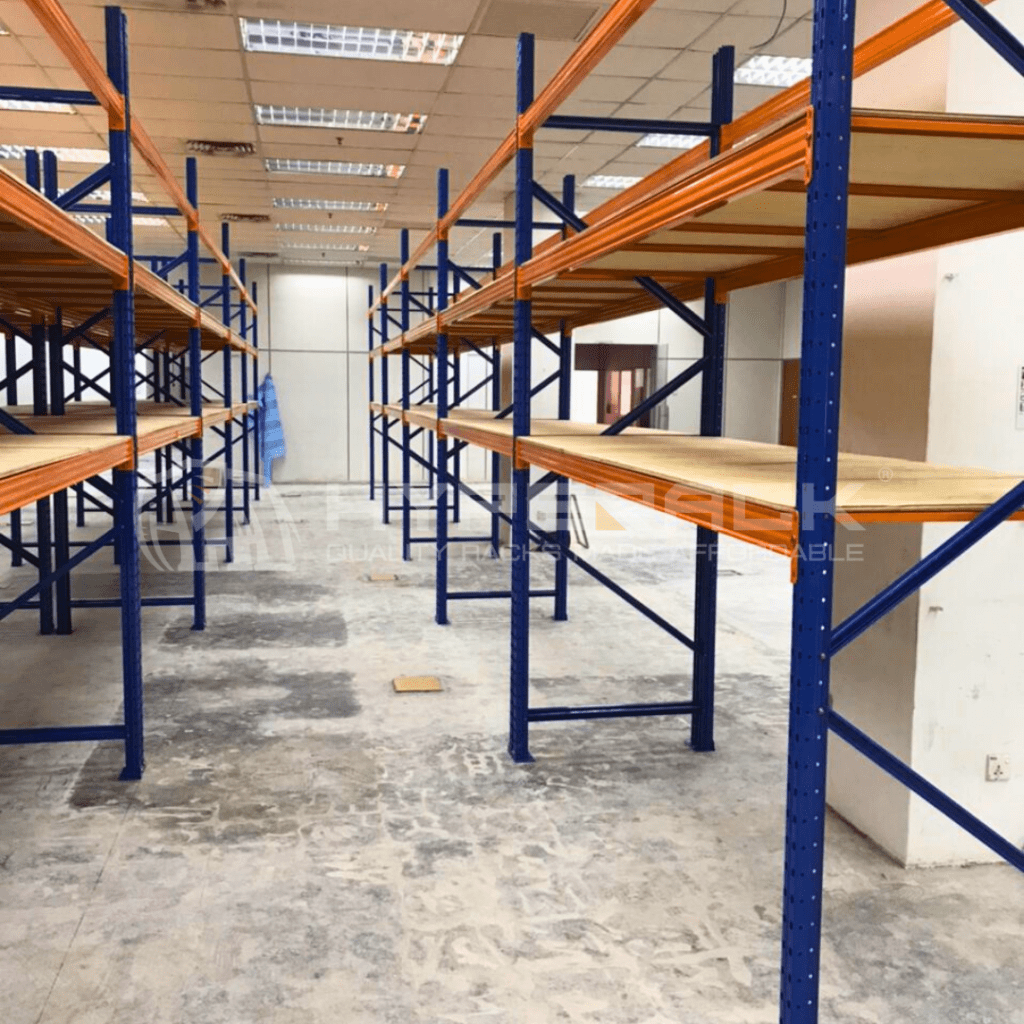
Medium and heavy-duty racking is designed to be practical, reliable, and efficient for various industries. Here’s what makes it stand out:
✅ Simple – Easy to use and maintain.
✅ Fast Install – Quick setup without complex procedures.
✅ No Extensive Training Required – Employees can easily adapt to the system.
✅ Durable & Long-Lasting – Built to withstand heavy loads and long-term use.
✅ Flexible & Scalable – Easily adjustable for evolving storage needs.
Proper racking solutions not only streamline daily operations but also contribute to a more organized and hazard-free workspace.
Selecting the Right Racking: A Quick Comparison
Choosing between medium and heavy-duty racking or others racking depends on your specific storage requirements:
Storage Need | Best Racking Type |
---|---|
Adjustable storage for smaller loads under 100kg | Light Duty Racking |
Up to 500kg per shelf | Medium Duty Racking |
Heavy, bulky materials | Heavy Duty Racking |
High inventory turnover | Racking Supported System |
Palletized storage and logistics | Racking System |
Understanding these factors helps in making an informed decision for long-term efficiency and safety.
Best Practices for Racking Installation & Maintenance
Choosing the right racking system is only the first step. Proper installation and regular maintenance ensure that your system remains safe and effective.
Installation Guidelines:
✔️ Plan Warehouse Layout – Optimize space before setting up racks.
✔️ Ensure Even Weight Distribution – Prevents overloading and imbalance.
✔️ Use Safety Features – Anchors, clips, and load indicators enhance stability.
Maintenance Best Practices:
✔️ Regular Inspections – Check for signs of wear, rust, or misalignment.
✔️ Train Staff on Proper Usage – Educate employees on safe loading/unloading techniques.
✔️ Follow Load Capacity Guidelines – Prevents overloading, which can lead to structural failure.
✔️ Schedule Periodic Safety Audits – Ensures compliance with industry standards.
By following these practices, businesses can extend the lifespan of their racking systems while maintaining a safe and efficient work environment.
Conclusion
Investing in the right racking system is key to optimizing storage, improving efficiency, and ensuring workplace safety. Whether you need medium-duty racking for flexible storage or heavy-duty racking for industrial loads, understanding the right system for your needs is essential.
A well-structured racking solution not only enhances daily operations but also helps in long-term cost savings and space management. Prioritizing the right racking setup ensures a more productive and organized workspace for years to come.
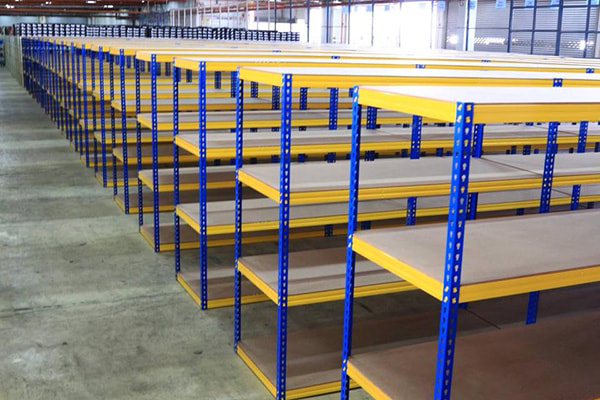
Boltless rack FAQ 2024
Boltless racks are a highly adaptable and user-friendly storage solution popular in warehouses, workshops, retail spaces, and even home garages. Built with a unique rivet or clip system, these racks offer strength and versatility without requiring bolts or screws. Whether you’re managing a commercial facility or organizing your tools at home, boltless racks provide a hassle-free, durable way to maximize storage space.
What Are Boltless Racks?
Boltless racks are a type of shelving system that requires no nuts, bolts, or screws for assembly. They use a rivet lock or clip system, making them easy to install and adjust without tools. Boltless racks are popular for their flexibility, strength, and ease of setup in both commercial and residential spaces.
How Boltless Racks Work?
Boltless racks use a rivet lock or clip system to securely connect beams and uprights, allowing easy assembly without any tools or hardware. Each shelf level clicks into place, creating a sturdy structure that can hold various weights depending on the rack type. This assembly process simplifies installation, making boltless racks ideal for businesses and homeowners who need a fast, flexible storage solution.
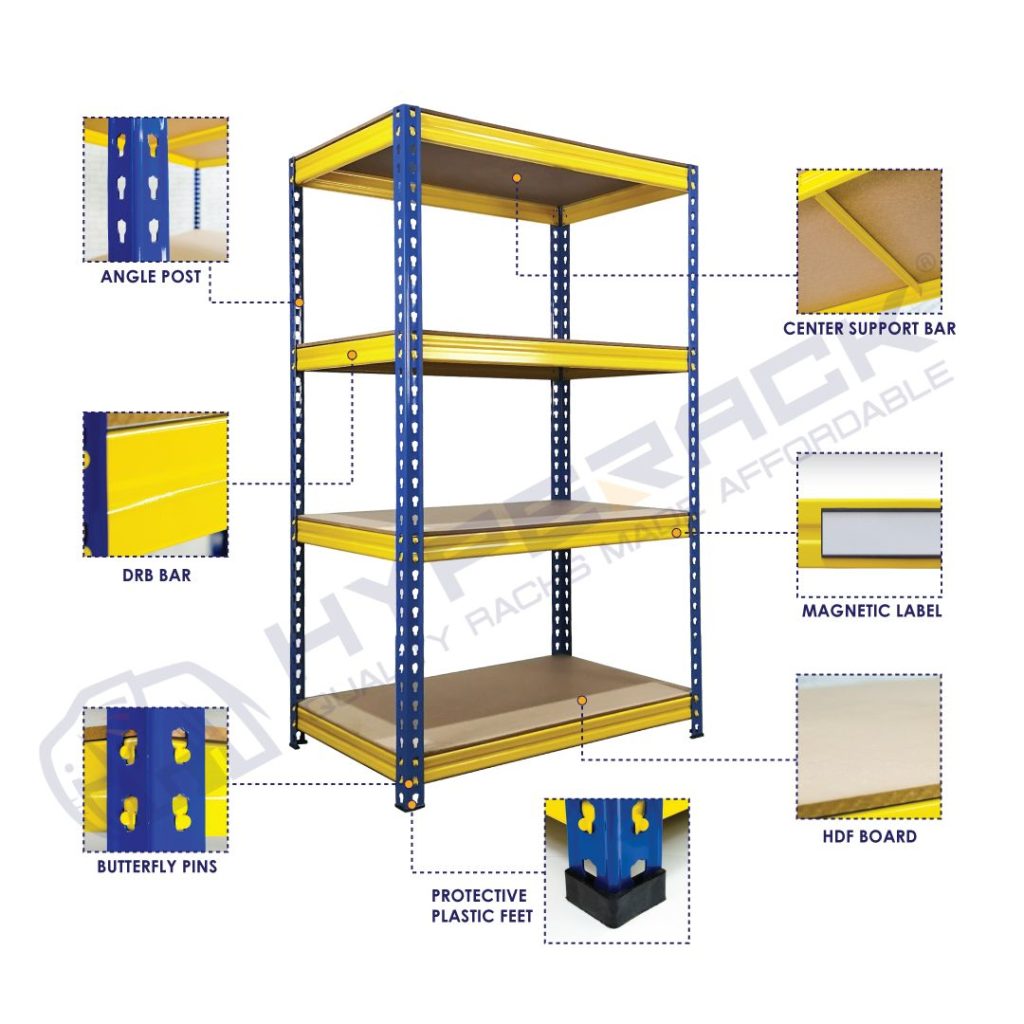
What Types of Boltless Racks Are Available?
There are several types of boltless racks to suit different needs:
- Heavy-Duty Boltless Racks: For industrial use, supporting large, heavy items.
- Medium-Duty Boltless Racks: Common in retail or smaller warehouses, balancing cost and strength.
- Light-Duty Boltless Racks: Ideal for home use, holding lighter items and storage boxes.
What Are the Main Benefits of Boltless Racks?
Boltless racks offer several unique advantages:
- Quick Assembly: Easy to put together without bolts or tools.
- Adjustability: Shelves can be moved up or down based on storage needs.
- Durability: Made with steel or aluminum, they offer long-lasting strength.
- Cost-Effective: Generally more affordable due to simplified design and assembly.
What Materials Are Boltless Racks Made From?
Most boltless racks are made from steel or aluminum for durability. Shelves can be made from materials like particleboard for light-duty use, or metal for heavier applications. Many boltless racks use recyclable materials, making them an eco-friendly option for storage.
Where Can Boltless Racks Be Used?
Boltless racks are versatile and can be used in a variety of settings:
- Warehouses: For storing inventory and heavy items.
- Retail: Ideal for backroom or display storage.
- Home Storage: Perfect for tools and equipment organization.
- Libraries and Archives: Useful for books, records, and files.
How Do I Install Boltless Racks?
Here’s a simple guide to installing boltless racks:
- Plan Layout: Determine where the racks will go and ensure enough space.
- Assemble Uprights and Beams: Insert beams into the uprights using the clip system.
- Add Shelves: Place shelves at your desired height.
- Secure if Needed: For added stability, especially with heavy-duty racks, secure to the floor or wall.
- Tutorial Video: Click Here
How Much Do Boltless Racks Cost?
The cost of boltless racks varies:
- Light-Duty Racks: Below RM100 – Check Here
- Medium-Duty Racks: Typically range from RM100–RM200 – Check Here
- Heavy-Duty Racks: Depending on size and material. Pricing depends on the rack’s weight capacity, material quality, and overall design. – Check Here
What Weight Can Boltless Racks Hold?
Boltless racks can handle a range of weights depending on their type:
- Light-Duty: Typically support up to 400kg totally, OR 100kg Per Level
- Medium-Duty: Can hold up to 800kg totally, OR 200kg Per Level
- Heavy-Duty: Often support over 1,600 kg totally., OR 400kg Per Level, but make sure to check the manufacturer’s specifications, as exceeding these limits can compromise the rack’s stability and durability.
Can I Use Boltless Racks Outdoors?
Yes, boltless racks can be used outdoors, but choose racks specifically designed or coated for outdoor use:
- Rust-Resistant Coatings: Look for powder-coated steel or galvanized racks for rust prevention.
- Weather Considerations: If exposed to rain or high humidity, protect shelves with waterproof covers or use metal shelving instead of particleboard, which may warp.
Do Boltless Racks Require Maintenance?
Although low-maintenance, boltless racks benefit from periodic checks:
- Inspect Joints: Ensure beams and uprights are securely locked to maintain load-bearing capacity.
- Dust and Clean: Regular cleaning, especially for food and retail storage, helps maintain hygiene and prolongs shelf life.
Can Boltless Racks Be Customized?
Yes, boltless racks offer various customization options to suit specific needs:
- Adjustable Shelves: Most boltless racks allow you to change the height of each shelf.
- Add-On Units: Some brands provide add-ons to expand storage capacity without buying a separate rack.
- Accessories: You can find bins, hooks, and dividers compatible with boltless racks to organize tools, small parts, or files.
Are Boltless Racks Flood-Resistant?
Boltless racks are not inherently flood-resistant, but certain modifications can improve their resilience in flood-prone areas:
- Material Choice: Opt for racks made from galvanized or powder-coated steel to resist rust and corrosion if they come into contact with water.
- Shelf Type: Use metal or wire shelving instead of particleboard or MDF, which can warp, swell, or degrade in high moisture.
- Elevated Placement: Where possible, place the racks on platforms or pallets to keep them above floodwater. This minimizes direct contact and protects stored items.
- Regular Maintenance: Inspect racks periodically, especially in flood-prone regions, to ensure there is no rust or weakening in the structure.
While these measures won’t make boltless racks entirely flood-proof, they can help improve their durability and longevity in damp or wet conditions.
Are Boltless Racks Fire-Resistant?
Boltless racks are not fireproof, but they can withstand certain levels of heat based on their materials:
- Metal Shelves: Metal shelves are more heat-resistant than wood or particleboard, which can burn or warp in extreme temperatures.
- Coated Steel: Powder-coated steel can withstand higher temperatures without degrading quickly, offering slight fire resistance. For storage areas that require fire resistance, such as industrial settings, consider using fully metal racks and ensuring the storage area has adequate fire safety measures.
How Long Can Boltless Racks Last?
The lifespan of boltless racks depends on several factors, including material quality, usage, and environmental conditions. Generally:
- High-Quality Steel Racks: When properly maintained, boltless racks made of high-quality steel can last anywhere from 90 to 200 years, especially in dry, indoor environments.
- Humidity and Corrosion: In humid or coastal areas, racks may need rust-resistant coatings, like powder coating or galvanization, to prevent corrosion. With these coatings, they can still last a decade or more.
- Load Capacity: Regularly loading racks close to or above their weight limit may cause structural fatigue over time, potentially shortening their lifespan. Heavy-duty racks used within their capacity limits are more likely to remain durable.
- Maintenance and Care: Regular inspections, cleaning, and proper storage practices can extend the life of boltless racks, as these reduce risks from rust or structural wear.
With proper care and ideal conditions, boltless racks are a long-lasting storage solution for homes, garages, warehouses, and retail spaces.
Are Boltless Racks Safe for Kids?
To make boltless racks safer in areas accessible to children, follow these safety precautions:
- Put Racks Close Walls: Prevent tipping by securing racks to walls, especially taller units.
- Keep Heavier Items on Bottom Shelves: Storing heavy items on lower shelves improves stability and reduces the risk of items falling from height.
- Edge Guards: Use rubber edge guards given to minimize the risk of injuries from sharp metal edges.
How Do Boltless Racks Compare to Traditional Bolt Racks?
Boltless racks are often chosen over traditional bolt racks for the following reasons:
- Faster Assembly: Without bolts, assembly is quicker and usually tool-free, making setup simple.
- Flexibility: Boltless racks allow for easy reconfiguration, while traditional bolt racks are more fixed.
- Cost and Convenience: Boltless racks are often more affordable and don’t require specialized tools, making them popular for both home and commercial use. However, traditional bolt racks may offer higher load capacities for certain heavy-duty industrial applications.
Can Boltless Racks Be Used for Hanging Items
Yes, boltless racks can be adapted for hanging items:
- Hooks and Hangers: You can install hooks or hangers on the shelves or beams of the rack to store items such as bags, coats, or tools.
- Adjustable Heights: The open design of boltless racks allows flexibility in the placement of hooks or rods, making them versatile for different types of hanging storage.
- Weight Limit: Always ensure that the weight of the hanging items does not exceed the weight capacity of the rack.
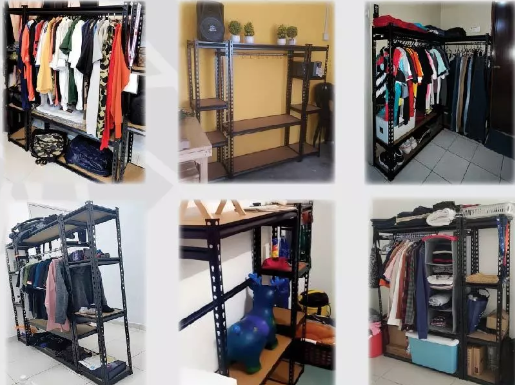
How Do Boltless Racks Perform in Cold or Hot Environments?
Boltless racks generally perform well in both cold and hot environments, but with some important considerations for extreme temperatures:
- Cold Environments:
- Material Considerations: In cold environments, such as freezers or refrigerated storage areas, it’s essential to choose racks made from corrosion-resistant materials, like stainless steel or galvanized steel. These materials can withstand the moisture and low temperatures typical of cold storage.
- Avoid Plywood or MDF Shelving: Shelving made from plywood or MDF (Medium-Density Fiberboard) may not perform well in extremely cold environments, as these materials can absorb moisture and become warped or damaged. Instead, opt for metal or other heat-resistant shelving options that are more durable and stable in freezing conditions.
- Rust Prevention: Moisture in cold environments can cause rust, so it’s crucial to maintain the racks in a dry state and check for any signs of corrosion. Regular maintenance can extend the life of the rack in cold conditions.
- Hot Environments:
- Heat-Resistant Materials: In high-temperature environments (such as industrial kitchens, factories, or areas near machinery), choose racks made of heat-resistant materials. Steel racks with heat-treated finishes or specialized coatings designed to withstand high temperatures are ideal. Avoid using materials like plywood, which can warp or degrade when exposed to extreme heat.
- Ventilation: The open design of boltless racks allows for good air circulation, which can be beneficial in hot environments to prevent heat buildup. Proper ventilation ensures that items are not subjected to prolonged heat exposure, which could lead to damage.
- Shelf Stability: In extremely hot conditions, ensure that the shelves are designed to handle the expansion or contraction of materials caused by temperature fluctuations. Metal racks with proper support structures will perform better in these environments.
In summary, boltless racks can perform well in both cold and hot environments if you choose the right materials. For cold environments, metal shelves are preferable over wood-based options, while for hot environments, ensure the racks are heat-resistant and have adequate ventilation. Avoid plywood and MDF in extreme temperatures to maintain the integrity of your racking system.
Are Boltless Racks Easy to Move?
Yes, boltless racks are typically easy to move, but there are a few considerations:
- Lightweight Construction: Many boltless racks are made of lightweight materials, making them easy to carry and reposition as needed.
- Disassembly and Reassembly: Because they are designed for easy assembly, you can often disassemble and reassemble the racks with little effort, which is convenient for moving them to new locations.
- Rolling Racks: Some boltless racks come with optional caster wheels, further improving mobility and ease of transportation.
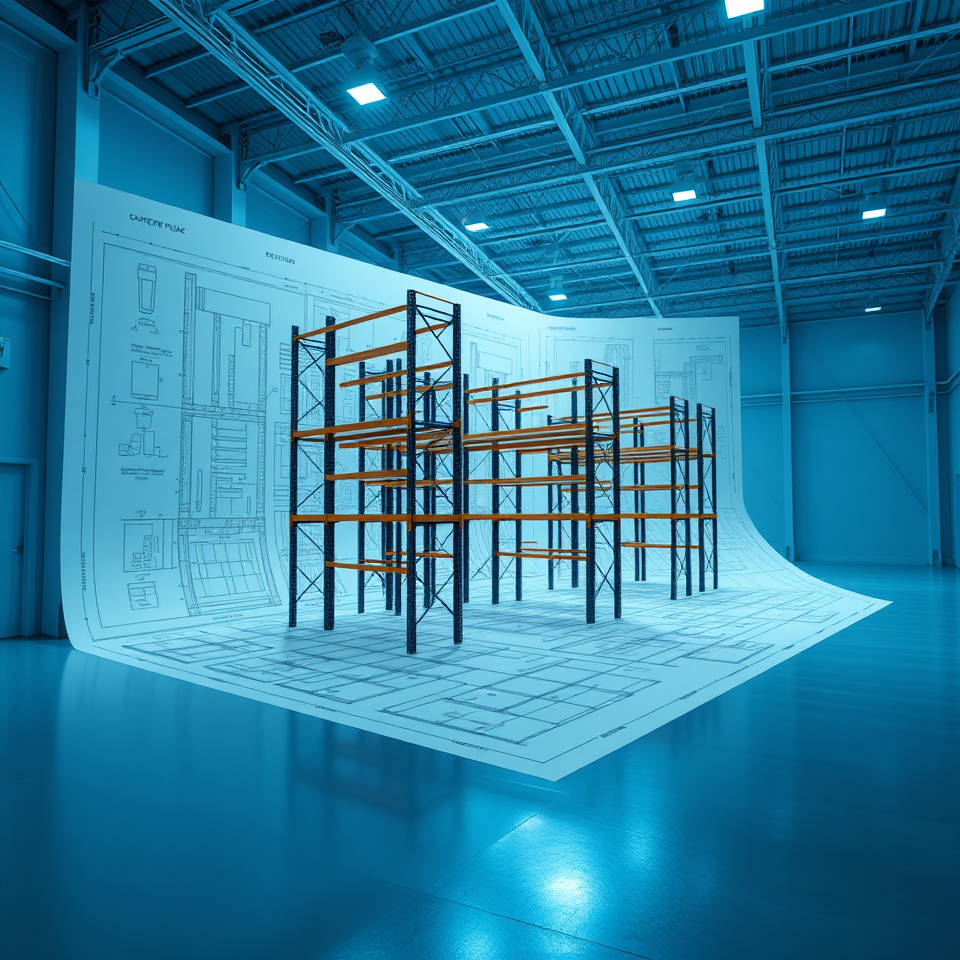
Ultimate Guide to Warehouse Racking Systems: Racking and Storage Solutions 2025
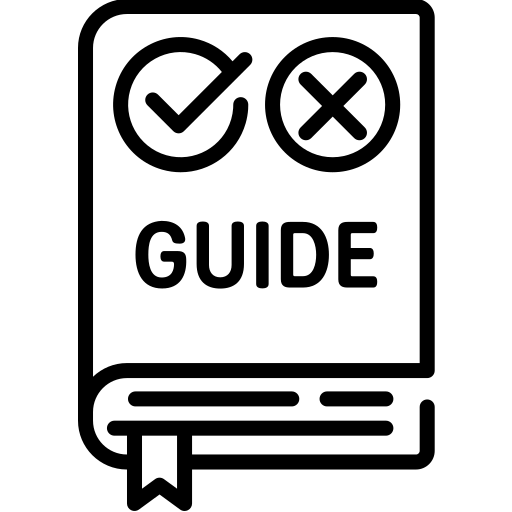
How to choose “Perfect” Racking System 2025
Imagine walking into your warehouse and seeing everything perfectly organized: rows of neatly stacked pallets, accessible inventory, and an efficient flow that saves you time and money. Sounds like a dream, right? A duty racking system that revolutionizes your storage. This guide is here to make that dream your reality. Whether you’re running out of space, dealing with inefficiencies, or just looking to modernize your operations, understanding warehouse racking systems could be the game-changer you need.
By the time you finish reading this, you’ll know how to choose the perfect heavy duty racking system for your needs, avoid costly mistakes, and unlock your warehouse’s full potential. Let’s dive in.
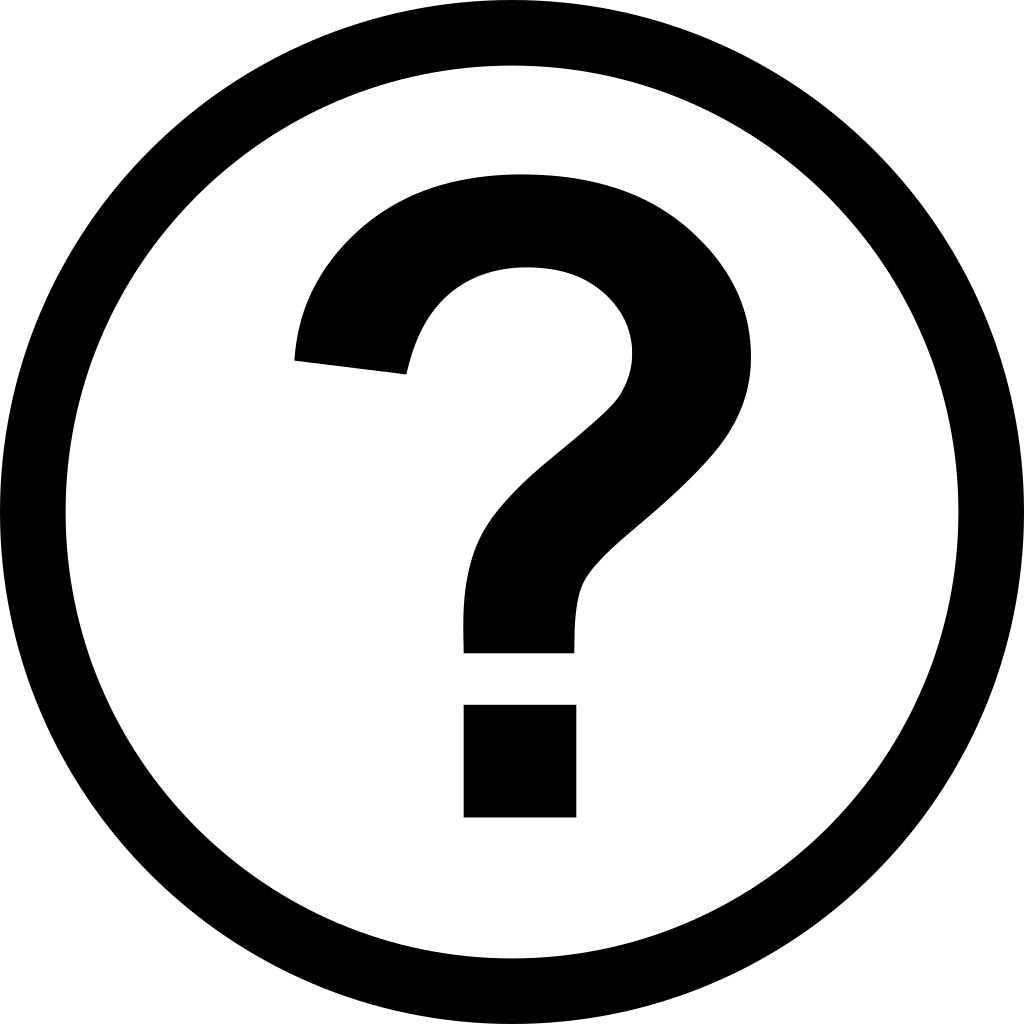
What Are Warehouse Racking Systems (And Why Should You Care)?
Warehouse racking systems aren’t just metal shelves—they’re the backbone of your commercial storage strategy. These systems optimize vertical space, helping you store more while using less square footage. But the benefits don’t stop there; investing in a heavy duty racking system can lead to significant long-term savings.
Your team spends less time hunting for products, your inventory stays secure, and your workflow improves dramatically. In today’s fast-paced logistics world, an efficient racking system isn’t optional—it’s essential for staying competitive and keeping customers happy.
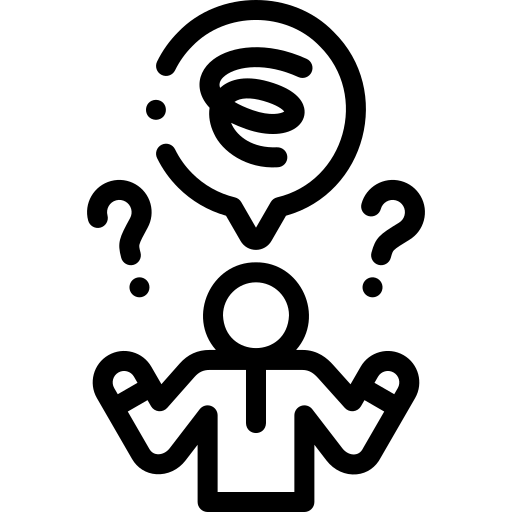
Are You Making the Most of Your Warehouse Space?
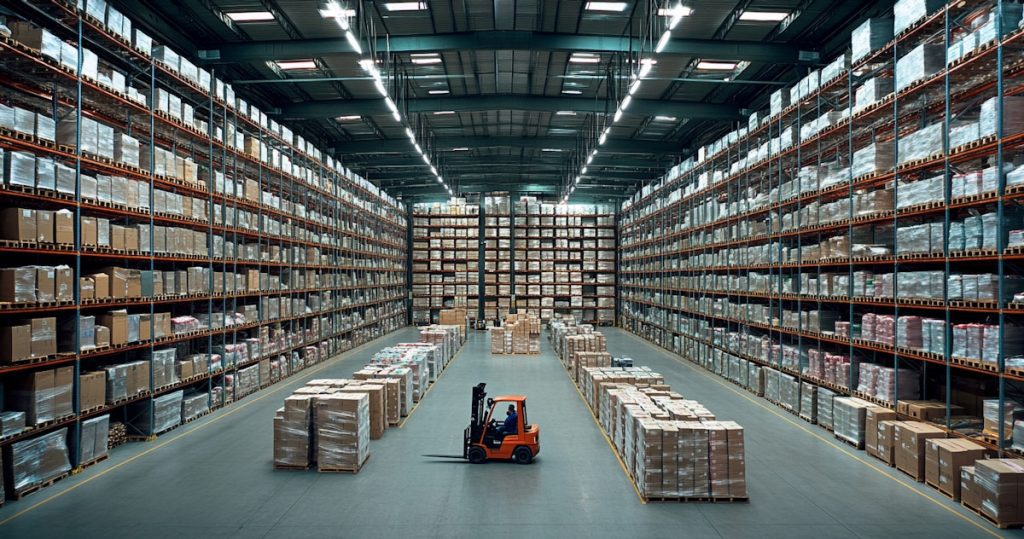
Here’s a question for you: When was the last time you evaluated your storage needs?
If you’re like most warehouse managers or business owners in Malaysia, you probably feel like you’re always running out of space. Stacking products on the floor might seem like a quick fix, but it often leads to wasted time, damaged goods, and frustrated workers.
The solution? A customized racking system tailored to your specific inventory needs can significantly enhance the storage of goods. By maximizing vertical space with innovative racking solutions, you can store up to 50% more inventory, which is crucial for any sale. seven layers of goods safely and securely. That means fewer headaches and more room to grow your commercial industrial business.
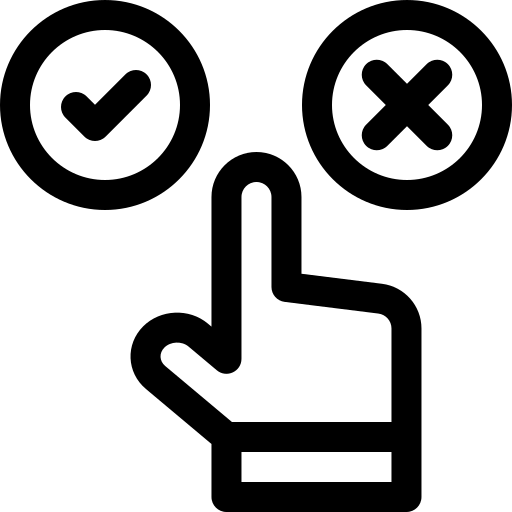
Unlock Your Warehouse’s Potential with the Right Racking System
When it comes to racking systems, one size doesn’t fit all; racking and shelving systems should be tailored to your specific needs. Here’s how to choose the right one:
1. Pallet Racking: Flexible and Easy to Access
Perfect for businesses with a wide variety of SKUs, this system gives you quick access to every pallet. No more wasting time or money searching for misplaced products.
2. Heavy-Duty Racking: Built for the Toughest Jobs
Need to store bulky, heavy items? Heavy-duty racking is your answer to maximizing storage density. These heavy-duty racking systems can handle loads exceeding 10,000 lbs., keeping your inventory safe and your operations running smoothly with regular racking inspections.
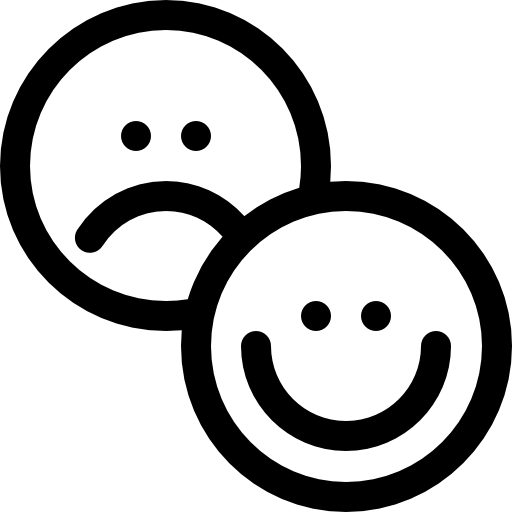
The Emotional Cost of Disorganization
Take a moment to think about how disorganization affects your team and how a proper racking inspection could help alleviate those issues. Frustration builds when workers can’t find what they need on the shelves, especially if the shelving rack is poorly organized, leading to inefficient storage of goods. Errors creep in when inventory isn’t where it’s supposed to be in your storage space. And let’s not forget the stress of dealing with damaged goods or missed deadlines, which can be alleviated with proper push-back racking.
Investing in a proper heavy-duty racking system isn’t just about storage—it’s about creating a platform where your team can thrive with efficient shelving racks and maximize the storage of goods. A well-organized warehouse boosts morale, improves safety, and sets the tone for a culture of efficiency and excellence.
Wait, hold your thought for a second—are you completely sure the racking system you’re considering is the best choice for your business?
There might be an even better option. Let’s chat, get the guide catalogue, and create a customized blueprint just for you with our free consultation campaign (starting now and available for the next 3 months)!
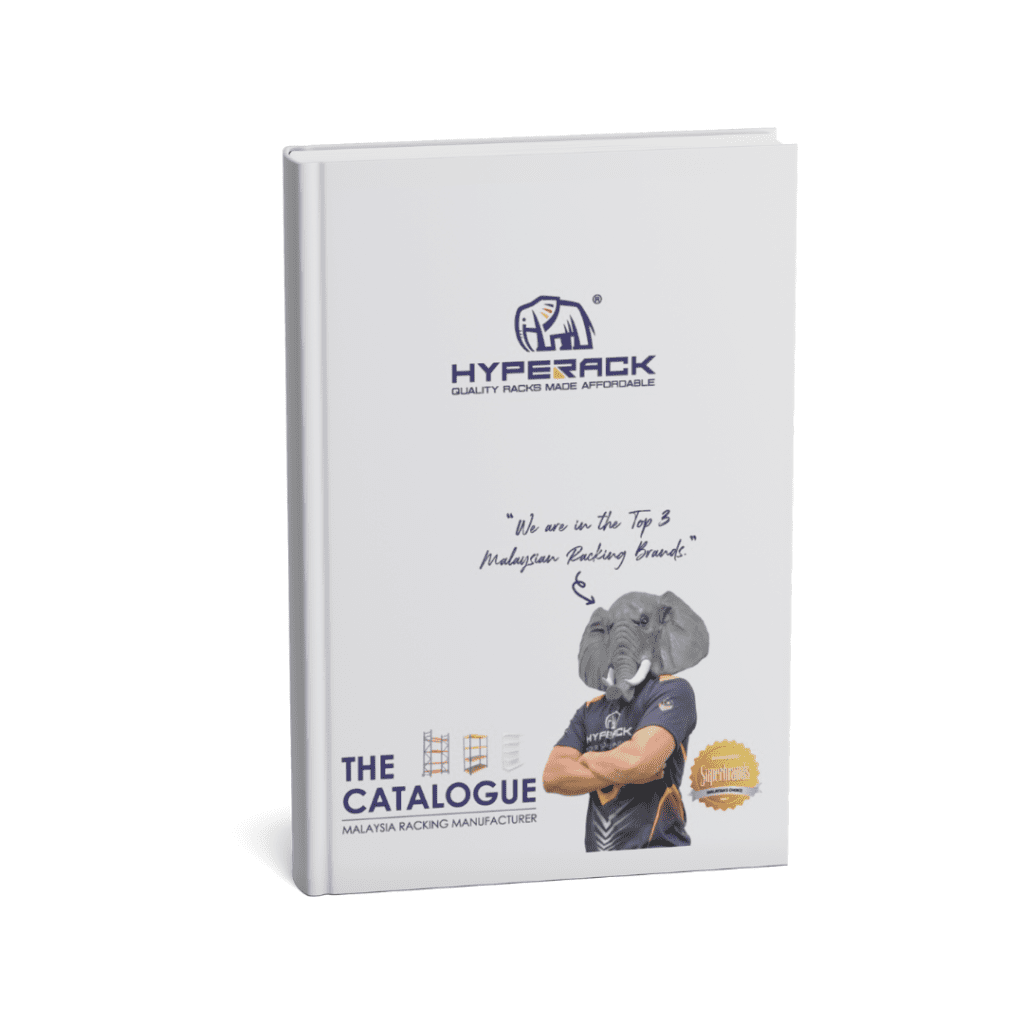
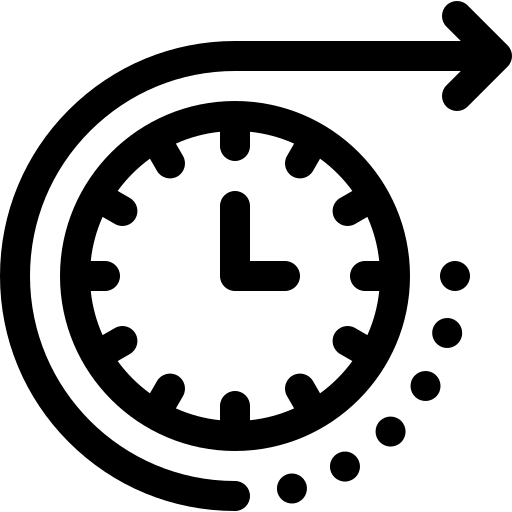
Why Automation is the Future (And Why You Can’t Afford to Ignore It)
Here’s a statistic that might shock you: Warehouses that implement automated storage and retrieval systems (ASRS) see an average of increased efficiency in the storage of goods. 30% improvement in efficiency and a significant reduction in labor costs.
Automation might sound intimidating, but think about this:
- Fewer mistakes lead to a more efficient storage system: Robots don’t misplace inventory.
- Faster operations: Goods are stored and retrieved in seconds with mobile shelving, improving overall workflow.
- Round-the-clock performance: No breaks, no downtime—efficient racking allows for continuous workflow in your operations.
If you want to stay competitive in 2025 and beyond, automation isn’t just an option—it’s your new secret weapon in the race of different types of warehouse management.
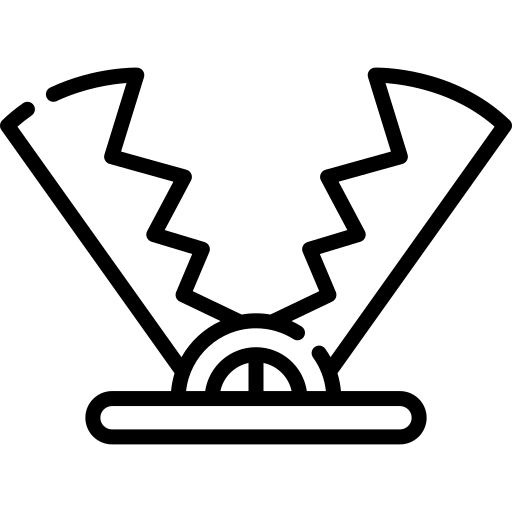
Are You Falling Into the “Cheap Solution” Trap?
We get it—budget matters when investing in new storage solutions. But here’s the hard truth: Cutting corners on your racking system can cost you more in the long run. Cheap systems might save you money upfront, but they often lead to costly mistakes in system design.
- Frequent repairs.
- Safety hazards.
- Inefficient use of space.
Instead, think of your racking system as an investment. A high-quality solution pays for itself through increased storage capacity, better workflow, and fewer disruptions.
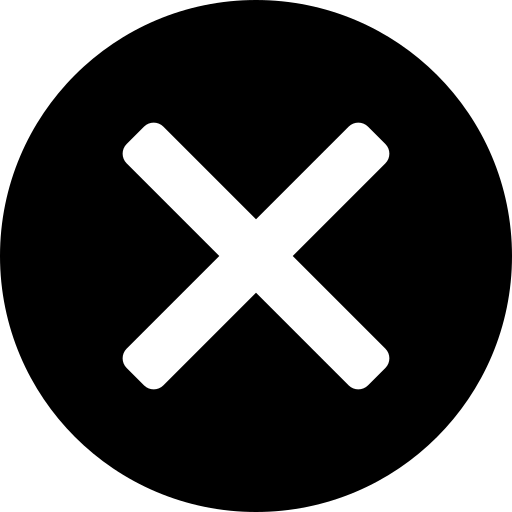
How to Avoid Common Mistakes When Choosing a Racking System
- Mistake #1: Not considering future growth.
Always choose a system that can scale with your business. You don’t want to outgrow your storage in two years. - Mistake #2: Not utilizing your heavy-duty storage rack effectively to maximize storage density in your automated warehouse. Overlooking safety in your industrial storage system can lead to serious consequences.
A racking system is only as good as its safety standards and how well it utilizes storage space. Look for systems that meet industry regulations and invest in proper training for your team to effectively utilize different types of warehouse racking. - Mistake #3: Choosing the wrong supplier.
Partner with a manufacturer that offers expert guidance, customization options, and reliable after-sales support.
Still unsure about the best solution for your business?
Let’s chat now for a FREE CONSULTATION and we’ll help you figure out exactly what you need!
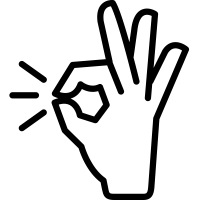
What Ideal Warehouse Lookalike
Close your eyes and imagine this: a heavy duty racking system that meets all your storage needs.
- Your team moving efficiently through a clean, organized warehouse.
- Pallets neatly stacked and easily accessible.
- Orders processed quickly, with no delays or errors, thanks to an efficient flow racking system and heavy-duty storage equipment.
- And most importantly, measurable ROI—fewer operational bottlenecks, faster order fulfillment, and reduced costs translating into better profits.
This isn’t just wishful thinking—it’s achievable with the right racking system. Every step you take toward optimizing your warehouse with selective racking brings you closer to this vision.
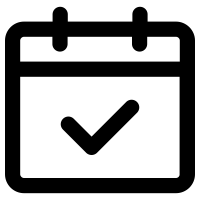
Future-Proof Your Warehouse Today
As we move into 2025, trends like sustainability, smart technology, and double-deep pallet racking are shaping the future of warehouse storage. Here’s how to stay ahead:
- Adopt IoT and AI in your factory to enhance your storage system. These technologies can track inventory in real time and predict maintenance needs, ensuring that your racking is commonly used to its fullest potential.
- Choose eco-friendly materials: Reduce your carbon footprint without compromising quality.
- Think modular: a flexible type of racking system can enhance your storage capabilities. Flexible systems can adapt to your changing needs, ensuring you always have the right type of racking system.
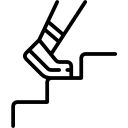
Your Next Step: Take Action Now
Don’t let inefficiencies hold you back. Your warehouse has untapped potential waiting to be unlocked with the right type of racking system. Here’s what you can do right now to optimize your storage space: consider implementing push-back racking for better accessibility.
- Evaluate your current system: What’s working? What isn’t?
- Contact a trusted supplier: Get expert advice on the best solutions for your needs.
- Start small if needed: Even minor upgrades to your pallet racking system can have a big impact on the overall efficiency of your storage of goods.
Your company deserves a warehouse that works as hard as you do, with efficient racking systems in place. By investing in the right racking system, you’re not just optimizing storage—you’re setting the stage for growth, efficiency, and success in your sales strategy.
Ready to transform your warehouse storage system with a heavy duty solution? The future is closer than you think—take the first step today towards upgrading to a better type of racking system.
How Hyperack Plan Your Racking System?
- Expertise: We dive deep into your warehouse space to determine the best racking configurations tailored to your needs.
- High-Tech Solutions: Our AutoCAD designs maximize storage while ensuring your team has ergonomic access to what they need.
- Side-by-Side Comparisons: Our planning process allows you to compare layout options easily, helping you make informed decisions.
- Data-Driven ROI Calculation: We provide detailed numerical data for each layout, empowering you to understand the impact on your bottom line.
- Customization: Our custom racking systems are built to meet any unique requirements, ensuring the best approach for any facility.
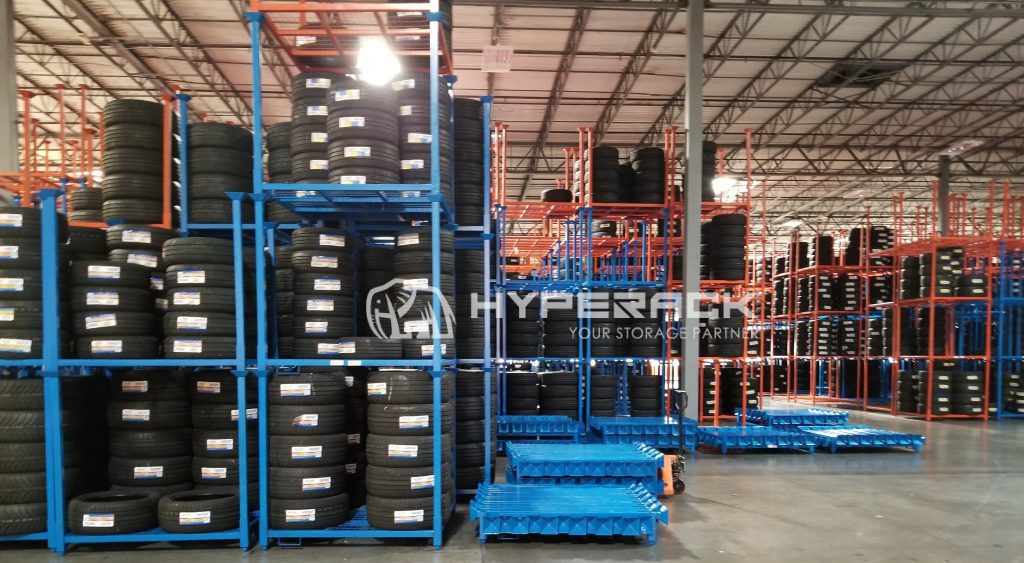
What is a Pallet Tainer?
What is a Pallet Tainer?
In this day, the Pallet Tainer has emerged as a key solution for enhancing storage and shipping efficiency. These strong, industrial containers designed to improve how businesses store and move items, making it a must-have for industries like agriculture, manufacturing, and logistics. Made from durable materials, Pallet Tainers fit neatly onto standard pallets, making them ideal for organized, space-efficient storage.
A Pallet Tainer designed to help businesses maximize warehouse space while protecting products from damage, dirt, and contamination. Thanks to their stackable design, these containers allow you to get the most out of your warehouse layout. Additionally, they are simple to move with forklifts or pallet jacks, making transportation a breeze. At Hyperack, we offer a wide selection of Pallet Tainers built to meet the demanding needs of warehouse operations.
How Does a Pallet Tainer Work?
You might wonder, what exactly is a Pallet Tainer and how does it work? Essentially, a Pallet Tainer is a robust container used for holding and storing goods on a pallet, making the entire process of transporting, stacking, and storing more efficient. Typically made of durable materials like plastic, steel, or wood, these containers are built to withstand heavy loads while providing easy access to stored items.
The design of the Pallet Tainer allows it to be securely placed on standard warehouse pallets, enabling smooth handling with forklifts or pallet jacks. Additionally, many Pallet Tainers come with features such as lids, handles, or stackability, further enhancing their versatility and efficiency in storage operations.
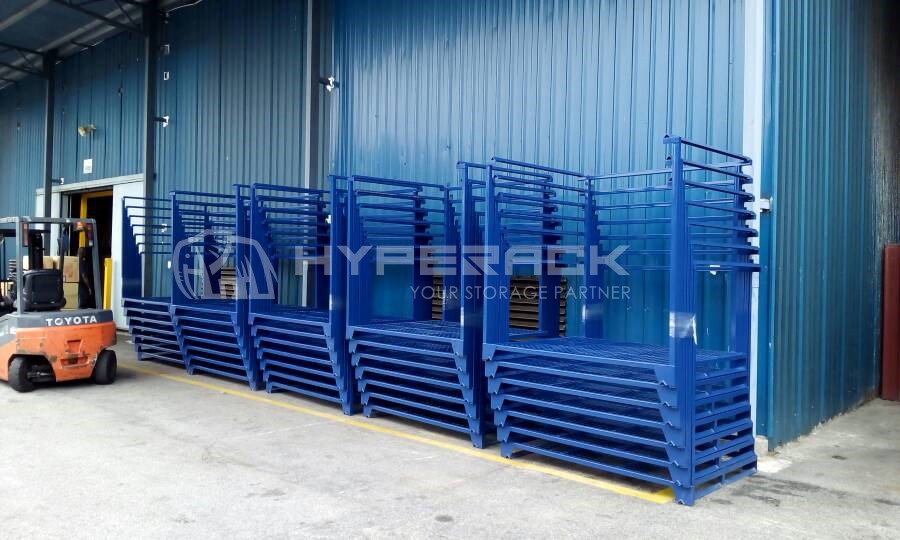
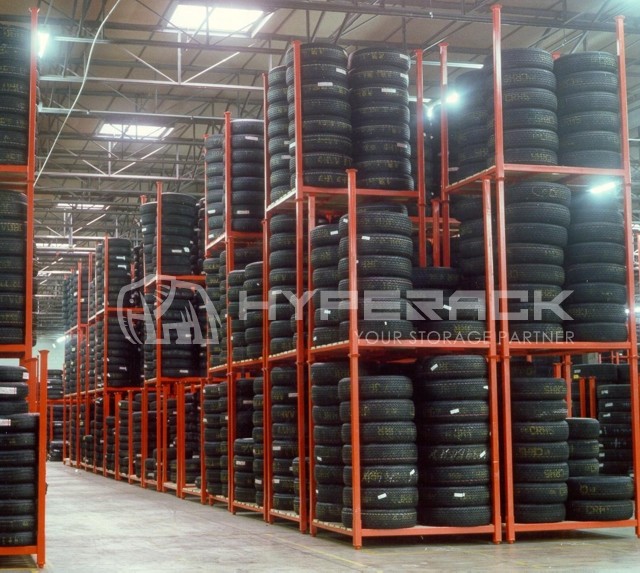
Benefits of a Pallet Tainer
Pallet Tainers offer numerous advantages that can significantly benefit your warehouse operations:
1. Space Efficiency
One of the primary benefits of using a Pallet Tainer is its space-saving design. These containers are stackable, allowing you to maximize vertical space in your warehouse. This feature is particularly valuable for businesses operating in facilities with limited floor space, as it helps to organize goods more effectively.
2. Durability and Protection
Pallet Tainers are designed to protect your products from damage during storage and transit. Whether you’re storing heavy industrial components or fragile goods, the sturdy construction of the Pallet Tainer ensures that your items remain safe and intact. Their enclosed design also prevents contamination, making them suitable for sensitive products.
3. Improved Handling
The standard size and shape of Pallet Tainers allow for efficient handling with forklifts or pallet jacks. This reduces manual labor and increases speed in both loading and unloading, helping to streamline warehouse operations and improve productivity.
4. Cost-Effectiveness
Using Pallet Tainers can lead to cost savings in several areas. With their ability to stack, reduce handling time, and minimize damage to products, these containers contribute to lower operational costs and higher efficiency.
5. Versatility
These containers are highly versatile, making them suitable for a wide range of industries, from agriculture to manufacturing to logistics. Moreover, they can be used to store everything from raw materials to finished goods, ensuring your inventory remains organized and easy to manage.
When to Use a Pallet Tainer?
You might be asking, when should I consider implementing Pallet Tainers in my warehouse? Here are some ideal scenarios:
- High-Volume Storage: If your business deals with large quantities of goods, Pallet Tainers are perfect for organizing and storing products in a way that maximizes space and reduces clutter.
- Diverse Product Types: If you manage multiple types of goods, the versatility of Pallet Tainers can help separate and store various products safely and efficiently, whether in the same or different locations.
- Transportation Needs: For businesses that need to move large quantities of goods across long distances, Pallet Tainers make shipping and handling smoother and more reliable.
Pallet Tainer vs. Other Storage Containers
When deciding on the best storage solution, it’s essential to understand how Pallet Tainers compare to other popular options in the market:
Feature | Pallet Tainer | Plastic Bins | Metal Cages | Wooden Crates |
---|---|---|---|---|
Durability | Very High | Medium | High | Medium |
Stackability | High | Low | High | Medium |
Cost | Moderate | Low | High | Low |
Flexibility | Very High | Low | Medium | Medium |
Best For | Efficient storage, transportation | Small parts storage | Heavy-duty items | Bulky items |
For example, while plastic bins might be more affordable, they do not offer the same durability and stackability as Pallet Tainers, making them less suitable for high-volume operations. Metal cages, while sturdy, can be bulky and difficult to stack, whereas Pallet Tainers excel in versatility and space efficiency.
Installation Guide for Using Pallet Tainers in Your Warehouse
Implementing Pallet Tainers in your warehouse is straightforward. Here’s a simple guide:
- Evaluate Your Needs: Assess your inventory types and determine whether Pallet Tainers are the best solution. Consider factors like product size, weight, and the need for stacking.
- Choose the Right Size: Pallet Tainers come in various sizes. Be sure to choose one that accommodates the dimensions of your products without wasted space.
- Optimize Your Storage Layout: Consider integrating Pallet Tainers into your existing racking system. Use shelving or racking that allows for easy access to stacked containers while maximizing vertical space.
- Monitor Product Movement: Track your goods efficiently to avoid overcrowding or product damage. Regularly inspect the condition of the Pallet Tainers to ensure they continue to meet your storage needs.
Cost of Implementing a Pallet Tainer System
The cost of Pallet Tainers can vary based on materials, size, and quantity. Generally, prices range from RM100. The cost will depend on the type of material chosen (plastic, metal, or wood) and additional features such as lids or stackability. Despite the initial investment, the long-term savings from improved space usage, reduced damage, and faster processing times make Pallet Tainers a cost-effective solution for most businesses.
Best Pallet Tainer Providers
When choosing a supplier for Pallet Tainers, look for the following:
- Reputation: Select a provider with a proven track record in offering high-quality Pallet Tainers. Check customer reviews to gauge their reliability.
- Customization Options: Opt for suppliers that offer customization, allowing you to tailor the containers to your specific warehouse needs.
- Warranty and Support: Look for providers who offer warranties and robust customer support, ensuring that your Pallet Tainers are built to last and backed by expert assistance.
Ready to enhance your warehouse efficiency? At HYPERACK, we specialize in double deep racking systems tailored to meet your specific needs, including the best Pallet Tainers. Contact us today for a FREE consultation, and let our experts help you optimize your storage solution! Explore our social media to see real-life projects in action.
Conclusion
In conclusion, Pallet Tainers provide an efficient, durable, and cost-effective storage solution for modern warehouses. By maximizing space, reducing handling time, and protecting goods, Pallet Tainers can significantly enhance warehouse operations, improve inventory management, and streamline transportation.
How Hyperack Plan Your Racking System?
- Expertise: We dive deep into your warehouse space to determine the best racking configurations tailored to your needs.
- High-Tech Solutions: Our AutoCAD designs maximize storage while ensuring your team has ergonomic access to what they need.
- Side-by-Side Comparisons: Our planning process allows you to compare layout options easily, helping you make informed decisions.
- Data-Driven ROI Calculation: We provide detailed numerical data for each layout, empowering you to understand the impact on your bottom line.
- Customization: Our custom racking systems are built to meet any unique requirements, ensuring the best approach for any facility.
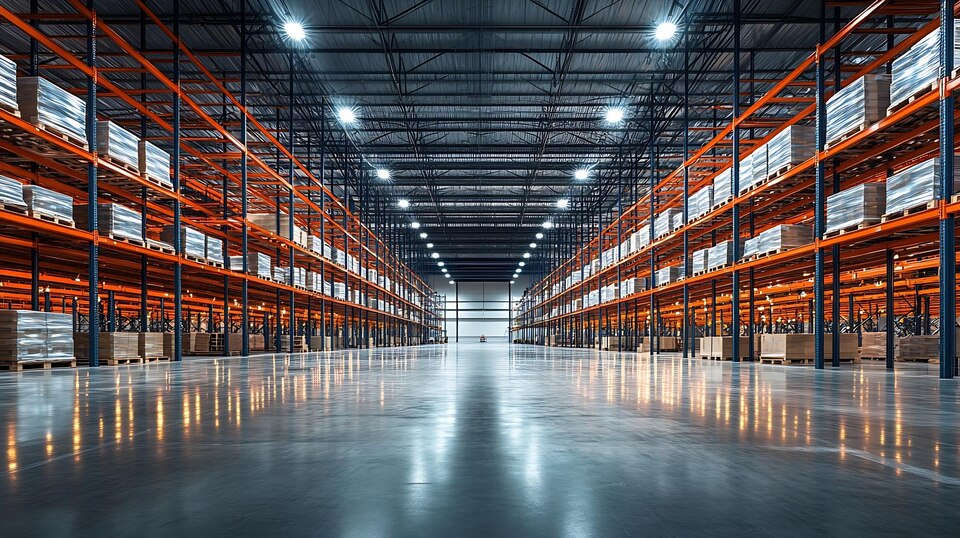
Cara Pilih Rak Gudang Terbaik di Malaysia 2025
Panduan Lengkap Memilih Rak Gudang Terbaik di Malaysia
Bila cakap pasal pengurusan gudang, mestilah semua orang nak pastikan stok tersusun dengan kemas, kan? Tapi, nak pilih rak gudang yang betul ni bukan senang, kalau salah pilih, boleh jadi satu hal. Kadang-kadang boleh jadi sakit kepala. Jom kita tengok apa jenis rak gudang yang sesuai dengan bisnes korang, dan macam mana nak pilih yang terbaik!
Apa Itu Rak Gudang?
Rak gudang bukan sekadar tempat untuk simpan barang—ia adalah asas untuk memastikan semua operasi gudang berjalan dengan lancar dan efisien. Secara ringkasnya, rak gudang adalah struktur penyimpanan yang direka untuk membantu susun barang dengan lebih sistematik. Dengan rak yang sesuai, ruang di gudang boleh dimanfaatkan sepenuhnya, dan barang-barang pun lebih mudah dicari dan diakses.
Pentingnya pemilihan rak gudang yang tepat bukan hanya terletak pada penjimatan ruang, tapi juga dalam mengurangkan kerosakan produk dan meningkatkan keselamatan pekerja. Bayangkan kalau gudang bersepah tanpa sistem penyusunan yang baik—ia bukan saja akan membuang masa, tapi boleh jadi risiko keselamatan. Rak gudang yang betul dapat mengurangkan kos operasi, jimatkan masa dan, paling penting, memastikan pekerja bekerja dalam persekitaran yang lebih selamat.
Bagaimana Rak Gudang Berfungsi?
Rak gudang bukan sekadar tempat simpan barang, ia adalah sebahagian daripada sistem yang lebih besar untuk memastikan semuanya berjalan lancar dan efisien. Mari kita lihat bagaimana komponen-komponen utama rak gudang bekerjasama:
- Rak Gudang: Ini adalah tempat utama untuk menyusun barang. Kebiasaannya, rak-rak ni dibuat daripada keluli atau bahan yang tahan lama untuk menampung barang yang berat. Ia bukan sahaja menyimpan, tetapi juga memaksimumkan ruang yang ada. So, gudang nampak lebih teratur dan barang boleh disusun lebih banyak dalam ruang yang lebih kecil!
- Sistem Pemindahan: Untuk memastikan barang sampai ke tempat yang betul, kita guna alat seperti forklift dan troli. Alat ni bergerak dengan mudah untuk pindahkan barang dari satu tempat ke tempat lain. Ia jimat masa sebab pekerja tak perlu lagi bergerak jauh untuk cari barang yang diperlukan. Mudah, kan?
- Sistem Pengurusan Gudang (WMS): Inilah otak kepada semuanya! WMS ni akan mengawal pergerakan semua barang dalam gudang. Bila barang dipindahkan, WMS terus kemas kini inventori secara automatik. Jadi, korang tak perlu risau tentang barang hilang atau stok yang tak dikemaskini. Semua jadi lebih pantas dan tepat!
- Pengaturan Ruang: Proses susun atur gudang dan rak ni penting untuk pastikan barang diletakkan pada tempat yang sesuai. Ada rak yang tinggi untuk simpan barang besar, dan ada juga yang sesuai untuk barang kecil. Dengan pengaturan yang betul, pekerja boleh capai barang dengan mudah dan cepat tanpa sebarang masalah.
Apabila semua ni bekerjasama, gudang korang akan jadi lebih pantas, teratur, dan efisien. Tapi macam mana pun, rak gudang ni tetap memerlukan penjagaan dan penyelenggaraan berkala supaya semua peralatan berfungsi dengan baik. Bila semua dalam keadaan terbaik, korang akan dapat operasi gudang yang smooth dan tak ada masalah.
Jenis-Jenis Rak Gudang Yang Korang Wajib Tahu
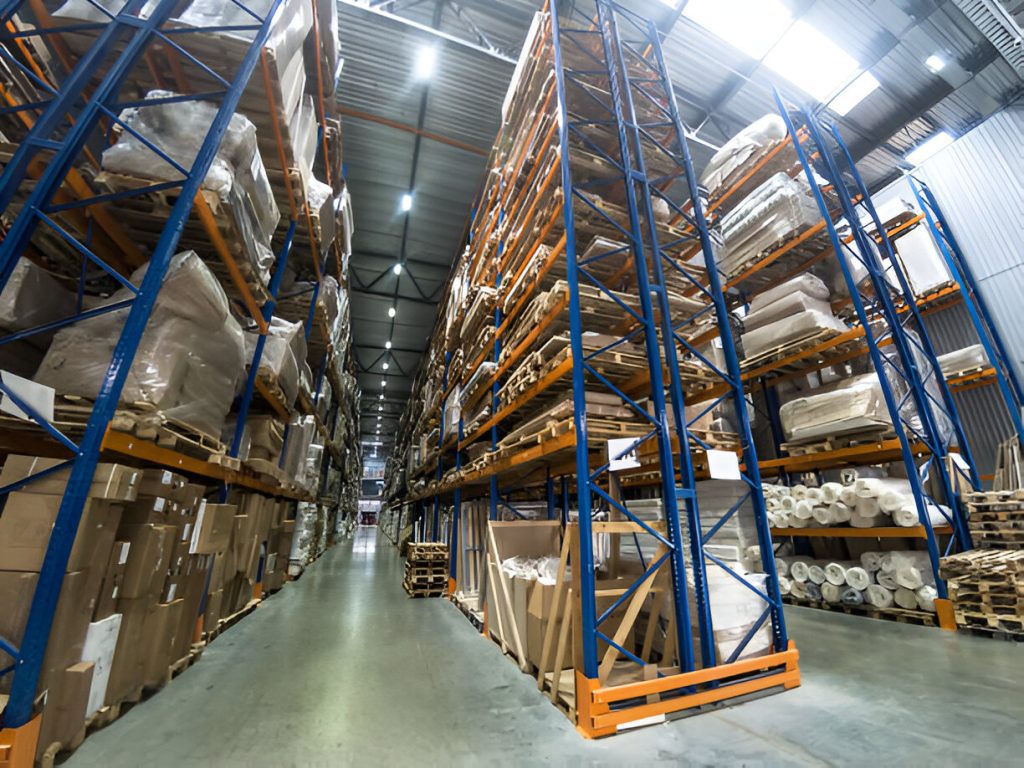
Rak Pallet (Pallet Racking): Rak ni memang pilihan utama kalau korang banyak stok atas pallet. Korang boleh pilih beberapa jenis rak, bergantung pada keperluan dan cara operasi gudang korang.
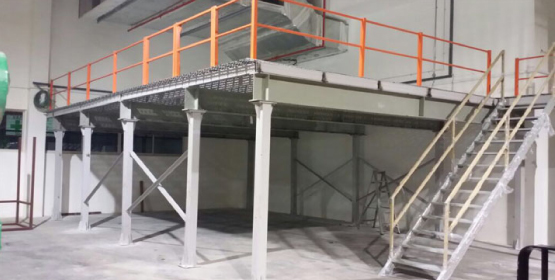
Rak Mezanin (Mezzanine Floor): Kalau gudang korang tinggi, rugi tak guna rak mezanin! Rak ni tambah ‘lantai kedua, ketiga sehingga bumbung’ dalam gudang tanpa perlu renovasi besar. Sangat sesuai untuk gudang yang ada banyak ketinggian, tetapi ruang lantai terhad. Dengan rak mezanin, korang boleh manfaatkan ruang secara lebih efisien.
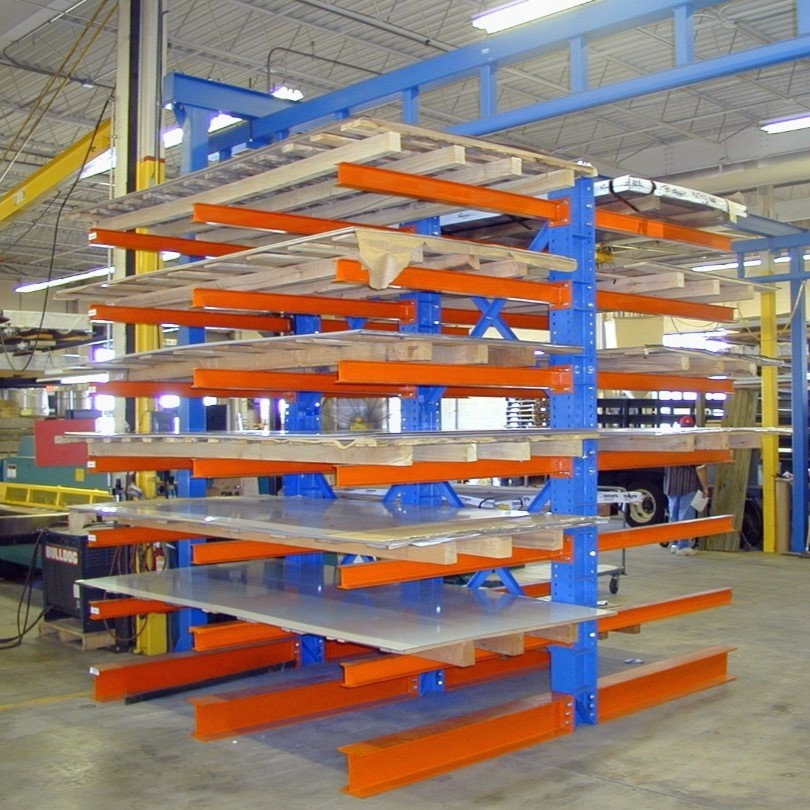
Rak Cantilever: Rak ni dikhaskan untuk barang yang panjang dan besar, seperti paip, kayu, atau bahan logam. Rak cantilever memberi fleksibiliti tinggi dan mudah untuk menyusun barang yang tidak boleh disusun dalam rak biasa. Sesuai untuk industri seperti pembinaan atau logistik, yang sering berurusan dengan barang yang panjang dan berat.
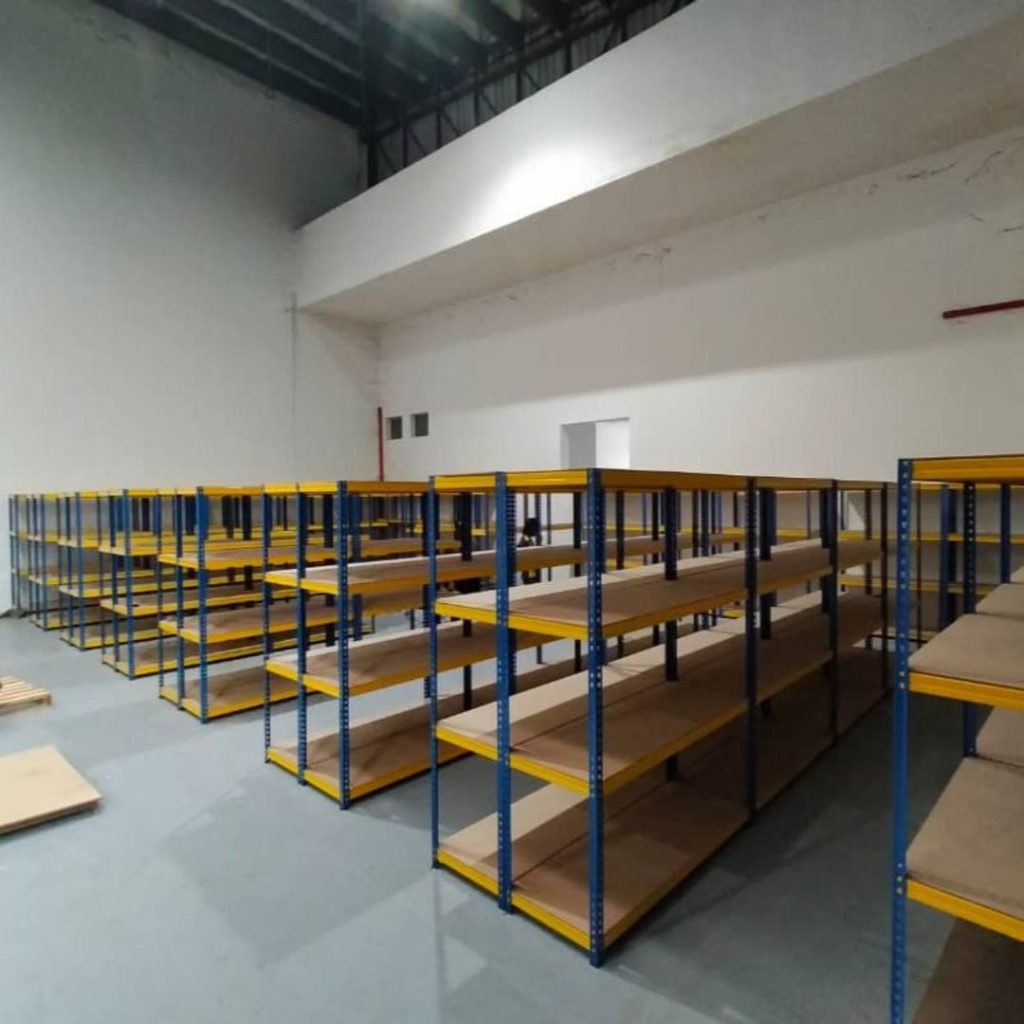
Rak Boltless: Rak ni memang paling mudah untuk dipasang. Tak perlukan skru, just snap and lock. Sesuai untuk menyimpan barang ringan seperti dokumen atau alat tulis. Kalau korang suka ubah susun atur mengikut keperluan, rak ni memang pilihan yang praktikal dan fleksibel.
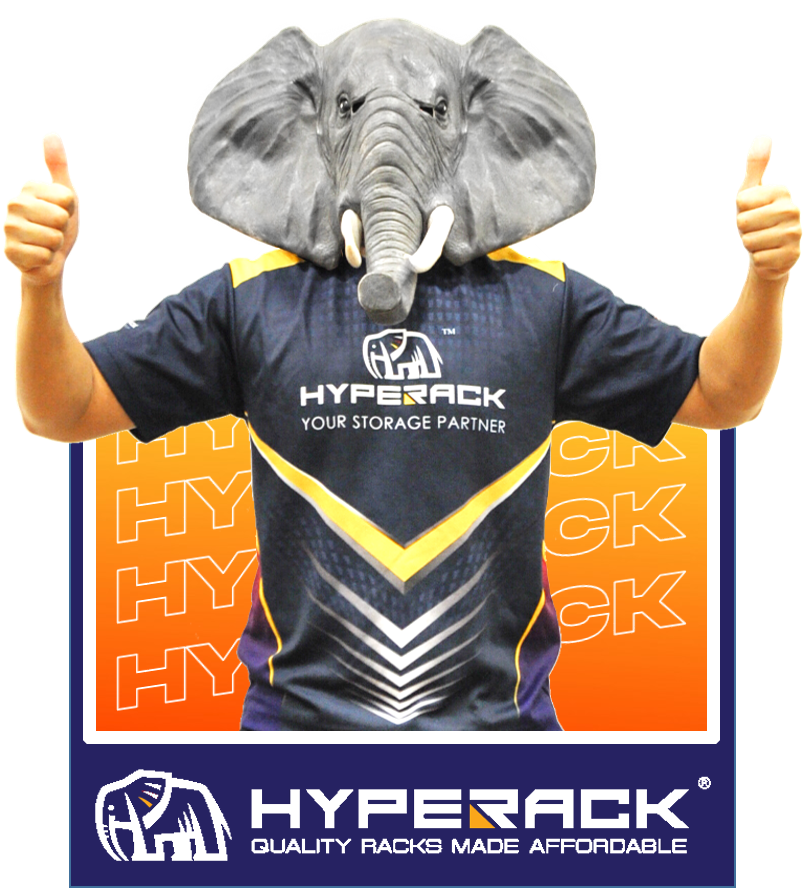
Jangan Biarkan Gudang Jadi Beban!
Hubungi kami sekarang untuk konsultasi percuma! Jangan biar gudang korang penuh dengan stok yang tak terurus. Dengan rak yang betul, korang boleh jimat ruang, tingkatkan produktiviti, dan pastikan barang korang selamat tersimpan. Pakar kami sedia bantu korang pilih sistem racking yang paling sesuai dengan keperluan gudang korang.
Manfaat Menggunakan Rak Gudang yang Tepat
Mungkin korang fikir rak gudang cuma tempat untuk simpan barang, tapi sebenarnya, rak yang betul boleh beri banyak manfaat besar untuk operasi harian bisnes korang. Kalau nak tahu, berikut adalah beberapa sebab kenapa memilih rak gudang yang tepat tu sangat penting:
- Ruang Lebih Teratur, Lebih Banyak Stok:
Dengan rak gudang yang direka dengan bijak, korang boleh memanfaatkan setiap inci ruang yang ada. Jadi, walaupun gudang korang tak terlalu besar, korang tetap boleh simpan lebih banyak barang. Ia bagaikan mengubah ruang sempit jadi lebih luas—betul-betul memaksimumkan potensi gudang korang! - Kerja Lebih Pantas, Hasil Lebih Banyak:
Bila rak gudang tersusun kemas, kerja jadi lebih mudah. Pekerja tak perlu lagi cari-cari barang lama-lama, semuanya ada di tempat yang sepatutnya. Semua ni membantu mereka bekerja lebih pantas, jadi lebih banyak pesanan boleh diselesaikan dalam masa yang singkat. Dengan rak yang betul, bisnes korang boleh berkembang lebih cepat! - Kurang Kesilapan, Lebih Tepat:
Siapa yang tak pernah buat silap kan? Tapi bila rak gudang teratur, risiko untuk pekerja buat kesilapan semakin berkurang. Stok lebih mudah dikesan, dan barang yang keluar atau masuk boleh dikelola dengan lebih tepat. So, korang boleh pastikan pelanggan terima barang yang betul pada masa yang tepat tanpa sebarang masalah. - Jimat Kos, Untung Lebih:
Memang betul, beli rak gudang berkualiti ni mungkin agak mahal pada permulaan. Tapi percayalah, pelaburan ni akan jimatkan kos korang dalam jangka panjang. Ruang disusun dengan lebih efisien, masa pun tak terbuang, dan yang paling penting, korang tak perlu risau pasal kerosakan barang atau kos penyelenggaraan yang tinggi. - Keselamatan Pekerja Terjaga:
Selain simpan barang, rak gudang yang betul juga melindungi pekerja korang. Kalau rak tersusun dengan baik, barang yang disusun takkan mudah jatuh atau menyebabkan kecederaan. So, korang bukan je jaga barang, tapi juga keselamatan pekerja, yang pastinya akan meningkatkan semangat kerja mereka.
Bilakah Anda Perlu Pertimbangkan Rak Gudang?
Rak gudang adalah pelaburan yang penting, tetapi ia lebih sesuai untuk bisnes yang menghadapi cabaran-cabaran tertentu. Jika bisnes anda berdepan dengan salah satu atau lebih daripada situasi berikut, rak gudang mungkin pilihan yang tepat untuk meningkatkan kecekapan operasi anda:
- Terlalu Banyak Stok yang Perlu Disusun
Jika bisnes anda mempunyai aliran barang yang tinggi, seperti syarikat e-dagang atau kedai runcit, rak gudang boleh membantu memaksimumkan ruang penyimpanan dan menjadikan proses pemilihan barang lebih cepat. Dengan rak yang sesuai, anda dapat menyusun stok dengan lebih teratur dan memudahkan pengambilan barang, menjimatkan masa dan usaha. - Ruang Gudang Terhad
Bagi mereka yang mengendalikan gudang di kawasan bandar atau di tempat dengan ruang terhad, rak gudang adalah penyelesaian yang bijak. Ia membolehkan anda memanfaatkan setiap inci ruang, dengan memilih rak yang sesuai seperti rak tinggi atau rak bertingkat. Ini menjadikan gudang kelihatan lebih teratur tanpa memerlukan pengubahsuaian besar. - Pengurusan Inventori yang Kompleks
Jika perniagaan anda melibatkan pelbagai jenis barang dengan keperluan penyimpanan yang berbeza atau memerlukan sistem inventori yang sangat tepat, rak gudang boleh disesuaikan untuk memenuhi keperluan anda. Sama ada barang berat atau besar, rak yang betul akan memudahkan pengurusan dan pengesanan stok, sekaligus mengurangkan risiko kehilangan atau kerosakan barang. - Keselamatan Pekerja yang Menjadi Keutamaan
Jika keselamatan pekerja adalah keutamaan anda, memilih rak gudang yang sesuai adalah langkah penting. Rak gudang yang direka dengan baik membantu meminimumkan risiko kecederaan, terutama apabila menyimpan barang berat atau tajam. Dengan rak yang stabil dan kukuh, anda juga mengurangkan kemungkinan rak terbalik atau runtuh, yang boleh menyebabkan kemalangan.
Rak Gudang vs Penyimpanan Lantai
Mungkin anda tertanya-tanya, mana satu yang lebih baik—rak gudang atau penyimpanan lantai? Perbezaannya sebenarnya besar, dan setiap pilihan datang dengan kelebihan dan kekurangannya tersendiri. Jom kita tengok perbandingan mudah antara kedua-duanya:
Ciri | Rak Gudang | Penyimpanan Lantai |
---|---|---|
Kos Permulaan | Lebih tinggi, tapi ada pulangan jangka panjang | Lebih murah, tapi kos penyelenggaraan boleh jadi tinggi |
Kecekapan Ruang | Sangat bagus—gunakan ruang secara menegak dan mendatar | Kurang efisien—ruang lantai banyak terbuang |
Kecepatan Akses | Cepat—barang boleh dicapai dengan mudah dan teratur | Biasa—barang di lantai kena angkat dulu |
Keselamatan | Tinggi—barang tersusun dengan selamat, kurang risiko kecederaan | Kurang—barang bersepah dan mudah terjatuh |
Fleksibiliti | Sesuai untuk semua jenis barang dengan pelbagai saiz | Sesuai untuk barang besar atau berat yang jarang perlu diakses |
Kekuatan dan Ketahanan | Kukuh—boleh tampung beban berat dan tahan lama | Kurang tahan lama—barang boleh rosak jika diletak sembarangan |
Contoh Mudah:
Bayangkan rak gudang sebagai rak buku yang tersusun rapi. Anda boleh susun barang dari bawah ke atas, menjadikan setiap inci ruang berfungsi dengan lebih baik. Sebaliknya, penyimpanan lantai lebih kepada meletakkan barang begitu sahaja atas lantai, yang bermaksud ruang lantai banyak terbuang. Ia lebih kepada “selagi ada ruang” dan kurang teratur.
Sekiranya anda ingin ruang yang teratur, mudah diakses, dan selamat, rak gudang memang pilihan terbaik. Memang kos awalnya mungkin lebih tinggi, tetapi jika dilihat dari segi jangka panjang, ia jauh lebih berbaloi. Penyimpanan lantai, walaupun lebih murah, cenderung menambah kerumitan dan risiko keselamatan kerana barang boleh bersepah dan mungkin rosak jika tidak disusun dengan betul.
Jadi, kalau anda nak gudang yang lebih teratur dan selamat, rak gudang sememangnya lebih berbaloi. Tetapi, kalau bajet anda terhad dan barang yang disimpan tidak terlalu banyak atau berat, penyimpanan lantai boleh jadi pilihan yang lebih praktikal.
Panduan Pemasangan Rak Gudang: Apa yang Perlu Dijangkakan
Memasang rak gudang bukanlah sekadar meletakkan rak baru di sudut gudang. Ia adalah proses yang memerlukan perancangan dan perhatian teliti untuk memastikan semuanya berfungsi dengan lancar dan dapat memenuhi keperluan operasi harian. Mari kita lihat langkah-langkah yang perlu diambil semasa memasang rak gudang.
- Menilai Ruang Gudang Anda: Sebelum mula, perkara pertama yang perlu dilakukan adalah memeriksa ruang gudang anda. Pastikan lantai cukup kukuh untuk menampung beban berat rak dan barang-barang yang akan disimpan. Ketinggian siling juga perlu dipertimbangkan – rak yang lebih tinggi memerlukan siling yang cukup tinggi untuk memberi ruang kepada pergerakan barang. Dan jangan lupa untuk memeriksa jika sistem elektrik dan rangkaian data sudah sesuai dengan sistem rak yang lebih canggih, terutamanya jika anda menggunakan sistem pengurusan gudang (WMS) yang memerlukan sambungan internet atau peranti lain.
- Memilih Sistem Rak yang Betul: Setelah ruang gudang dinilai, sekarang tiba masanya untuk memilih rak yang sesuai dengan keperluan anda. Pemilihan rak yang tepat akan membuatkan penyimpanan barang lebih teratur dan efisien. Jika anda menyimpan barang yang lebih berat, rak pallet mungkin pilihan terbaik. Tetapi, jika barang anda mempunyai pelbagai saiz, rak longspan atau boltless mungkin lebih sesuai. Ada juga situasi di mana anda memerlukan penyelesaian rak yang disesuaikan khas, jadi pastikan anda memilih apa yang terbaik untuk jenis produk dan ruang gudang yang ada.
- Integrasi dengan Sistem Pengurusan Gudang (WMS): Jika anda menggunakan sistem pengurusan gudang (WMS) untuk mengawal aliran inventori dan operasi harian, pastikan rak yang baru dipasang dapat berintegrasi dengan sistem tersebut. Ini penting untuk memantau stok secara real-time dan memastikan bahawa proses pemilihan dan penyimpanan barang berjalan dengan lancar. Dengan integrasi yang baik, anda boleh mengelakkan kesilapan manusia dan meminimumkan kesilapan semasa operasi, menjadikan gudang lebih efisien.
- Pemasangan dan Pengujian Rak Gudang: Setelah segala persediaan dilakukan, kini tiba masanya untuk memasang rak. Pasukan pemasangan akan memastikan bahawa rak dipasang dengan betul, dan pastikan rak tersebut kukuh dan stabil. Mereka akan menyesuaikan rak dengan spesifikasi yang telah dipersetujui, memeriksa kesesuaian ruang penyimpanan dengan produk yang akan diletakkan di dalamnya. Proses ini juga akan melibatkan pengujian sistem untuk memastikan semuanya berfungsi dengan lancar – mana-mana isu kecil yang timbul semasa pemasangan akan ditangani segera supaya tidak mengganggu operasi di kemudian hari.
- Penyelenggaraan Berkala dan Pemeriksaan: Setelah rak dipasang dan berfungsi, tugas anda tidak berakhir di situ. Untuk memastikan rak sentiasa dalam keadaan baik dan berfungsi dengan efisien, penyelenggaraan berkala adalah kunci. Pastikan anda memeriksa rak dan komponen-komponennya secara rutin, terutamanya jika rak tersebut digunakan untuk menyimpan barang berat atau sering disusun semula. Lakukan pemeriksaan untuk memastikan rak tidak rosak atau longgar. Jangan lupa untuk memastikan sistem pengurusan gudang sentiasa dikemas kini supaya proses beroperasi dengan lancar dan tanpa masalah. Penyelenggaraan yang konsisten bukan sahaja memastikan keselamatan pekerja, tetapi juga memanjangkan jangka hayat rak anda.
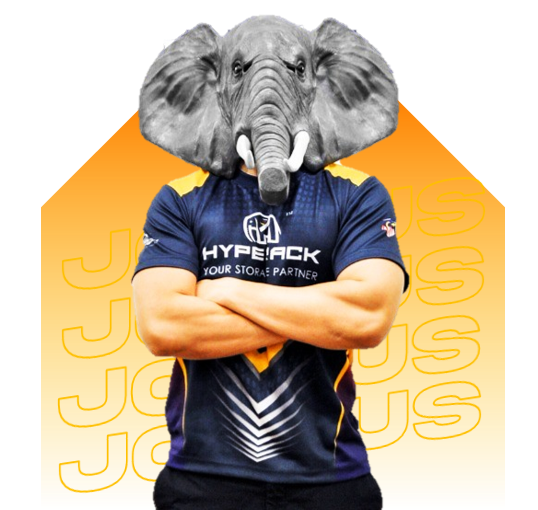
Gudang lebih tersusun, perniagaan lebih lancar
Gudang serabut, kerja lambat? Kami ada penyelesaian! Racking terbaik untuk gudang lebih tersusun, stok mudah cari, dan perniagaan lebih lancar. Hubungi kami sekarang!
Berapakah Kos Rak Gudang?
Kos rak gudang sebenarnya bergantung pada beberapa faktor, termasuk jenis rak yang anda pilih, saiz gudang, dan keperluan khusus untuk perniagaan anda. Walaupun kos awal mungkin nampak agak tinggi, rak yang tepat boleh memberi banyak manfaat dan pulangan yang berbaloi dalam jangka panjang. Jadi, walaupun ia merupakan pelaburan, rak gudang yang betul dapat membantu memudahkan operasi, jimatkan masa, dan pastikan keselamatan barang serta pekerja.
Berikut adalah anggaran harga untuk pelbagai jenis rak gudang yang biasa digunakan:
- Rak Gudang Kecil: RM500 hingga RM5,000
Untuk perniagaan kecil yang tidak memerlukan ruang penyimpanan yang besar atau sistem yang kompleks, rak jenis boltless atau longspan adalah pilihan yang sesuai. Kosnya lebih rendah dan sangat berguna untuk barangan yang ringan atau saiz sederhana. - Rak Gudang Sederhana: RM5,000 hingga RM50,000
Jika perniagaan anda memerlukan rak yang lebih besar dan lebih fleksibel, seperti rak pallet atau rak selective pallet racking, kosnya akan sedikit lebih tinggi. Rak jenis ini sesuai untuk perniagaan yang mempunyai stok dalam kuantiti yang lebih banyak dan perlukan kemudahan akses yang cepat. - Rak Gudang Kompleks: RM50,000 hingga RM200,000
Untuk perniagaan yang memerlukan sistem penyimpanan yang lebih besar atau lebih canggih, seperti rak mezanin atau rak cantilever, kosnya akan lebih tinggi. Rak jenis ini sesuai untuk operasi yang lebih besar dan memerlukan keupayaan penyimpanan tambahan atau barangan yang lebih berat dan panjang.
Selain itu, kos rak gudang juga boleh melibatkan perbelanjaan tambahan untuk pemasangan, penyelenggaraan, dan ciri keselamatan seperti pelindung tiang. Walaupun harganya mungkin lebih tinggi, memilih rak yang betul dapat membantu perniagaan anda lebih efisien dan mengurangkan kos jangka panjang dengan meminimumkan kerosakan dan meningkatkan pengurusan inventori.
Memilih Penyedia Rak Gudang yang Tepat
Memilih penyedia rak gudang yang betul adalah salah satu keputusan penting yang boleh membantu gudang korang beroperasi dengan lebih lancar dan efisien. Rak yang betul boleh buat perbezaan besar, bukan saja dari segi susunan barang, tapi juga keselamatan dan produktiviti pekerja. Jadi, macam mana nak pilih penyedia rak yang sesuai? Jom tengok beberapa tips yang boleh bantu korang buat pilihan yang bijak!
- Cari Pakar Tempatan yang Berpengalaman : Mula dengan cari syarikat yang dah berpengalaman di Malaysia. Syarikat tempatan biasanya lebih faham cabaran dan keperluan gudang di sini, jadi mereka boleh bagi penyelesaian yang lebih tepat dan sesuai dengan kondisi tempatan. Lagi satu, syarikat tempatan ni mudah dihubungi dan boleh beri servis yang lebih pantas kalau ada masalah.
- Periksa Sijil dan Piawaian : Jangan lupa pastikan penyedia rak yang korang pilih tu memenuhi piawaian kualiti yang tinggi. Rak gudang perlu tahan lasak dan selamat untuk digunakan dalam jangka masa panjang. Kalau rak tu tak cukup kuat atau selamat, bukan saja kos nak repair tinggi, malah keselamatan pekerja pun terancam. Jadi, pastikan rak yang ditawarkan memenuhi semua syarat ketahanan dan keselamatan yang ditetapkan.
- Pilih Penyedia yang Ada Sokongan Penuh : Yang ni penting! Cari penyedia yang bukan hanya jual dan pasang rak je, tapi juga sediakan sokongan selepas jualan. Mereka patut bagi nasihat sebelum pemasangan, pastikan pemasangan rak berjalan lancar, dan kalau ada masalah, mereka boleh bantu dengan cepat. Dan yang lebih penting, pastikan mereka ada latihan untuk pekerja supaya mereka tahu cara guna rak dengan selamat.
- Bandingkan Harga dan Jaminan : Jangan mudah terpedaya dengan harga yang terlalu murah. Memang, kita semua nak berjimat, tapi pastikan korang dapat harga yang berbaloi dengan kualiti dan servis yang ditawarkan. Sebelum buat keputusan, dapatkan sebut harga daripada beberapa pembekal, bandingkan harga dan jaminan yang mereka bagi. Pilih penyedia yang boleh beri jaminan kualiti dan servis selepas jualan yang baik.
Dah bersedia nak upgrade gudang korang?
Di HYPERACK, kami pakar dalam menyediakan sistem rak gudang yang disesuaikan mengikut keperluan bisnes korang. Hubungi kami hari ini untuk sesi perundingan PERCUMA, dan biarkan pakar kami bantu korang cari penyelesaian penyimpanan yang terbaik! Nak tengok projek-projek kami yang dah berjaya? Lihat di media sosial kami!
Kesimpulan
Rak gudang bukan sekadar peralatan biasa; ia adalah langkah penting untuk mewujudkan gudang yang lebih cekap dan teratur. Dengan memilih rak yang sesuai, anda bukan sahaja dapat mengoptimumkan ruang gudang, tetapi juga meningkatkan keselamatan serta mengurangkan kos operasi jangka panjang. Rak yang tepat membolehkan proses penyimpanan dan pengambilan barang menjadi lebih pantas, meningkatkan produktiviti dan mengurangkan kesilapan manusia.
So, persoalan sebenar bukanlah ‘Adakah saya perlu menggunakan rak gudang yang sesuai?’—tetapi lebih kepada ‘Bilakah masa yang tepat untuk memilih rak yang betul bagi masa depan perniagaan saya?”
Bagaimana Hyperack Merancang Sistem Rak Anda?
- Kepakaran Kami: Kami akan menyelami ruang gudang anda dan fahami sepenuhnya keperluan anda, untuk merancang sistem rak yang paling sesuai dan efektif.
- Penyelesaian Teknologi Canggih: Rekaan AutoCAD kami memastikan ruang penyimpanan dimanfaatkan sepenuhnya.
- Perbandingan Susun Atur: Kami memudahkan anda untuk membandingkan pelbagai pilihan susun atur, supaya anda boleh buat keputusan yang paling tepat.
- Pengiraan ROI Berdasarkan Data: Kami menyediakan data yang jelas dan terperinci bagi setiap susun atur, supaya anda boleh lihat kesan langsung terhadap keuntungan perniagaan anda.
- Kustomisasi Mengikut Keperluan: Sistem rak yang kami sediakan boleh diubahsuai untuk memenuhi keperluan khusus, memastikan penyelesaian terbaik untuk setiap jenis kemudahan.
Soalan Lazim (FAQ)
Berapa lama rak gudang boleh tahan?
Rak berkualiti tinggi mampu bertahan lebih dari 10 tahun jika dijaga dengan baik. Pastikan rak tidak terlebih beban dan sentiasa bersih.
Adakah rak gudang perlu diselenggara?
Ya, rak perlu diperiksa secara berkala untuk memastikan keadaan baik dan tidak rosak. Pemeriksaan setiap 6 bulan adalah disarankan.
Adakah rak pallet sesuai untuk semua jenis barang?
Rak pallet lebih sesuai untuk menyimpan barang berat atau dalam kuantiti banyak. Pastikan untuk memilih jenis rak pallet yang tepat mengikut keperluan.
Perlukah pemasangan profesional untuk rak gudang?
Kebanyakan pembekal menawarkan perkhidmatan pemasangan. Pastikan anda bertanya mengenai kos pemasangan semasa membeli.
Bolehkah rak gudang diubah suai mengikut keperluan?
Ya, kebanyakan rak gudang seperti rak boltless atau rak pallet boleh diubah suai mengikut ketinggian atau saiz untuk menampung keperluan penyimpanan yang berbeza.
Adakah rak gudang tahan karat?
Kebanyakan rak berkualiti tinggi dilengkapi dengan lapisan salutan anti-karat, terutamanya jika digunakan dalam persekitaran lembap atau gudang sejuk.
Adakah terdapat jaminan untuk rak gudang?
Kebanyakan pembekal menawarkan jaminan produk, biasanya 1-5 tahun bergantung pada jenama dan jenis rak. Jangan lupa bertanya tentang terma jaminan semasa membeli.
Ada sebarang soalan? Jangan ragu untuk mesej kami terus! Jom berbincang lebih lanjut dan dapatkan Konsultasi Percuma.